Introduction
In Australia, shipbuilding plays a vital role in the economy, creating job opportunities and fostering growth. Welding, as a crucial aspect of shipbuilding, ensures the structural integrity of vessels.
It is responsible for joining and strengthening various components, such as hulls and decks. The importance of welding in shipbuilding cannot be overstated as it guarantees the safety and durability of the ships.
Without welders, the construction process would be incomplete, leading to compromised functionality and reliability. Additionally, welding in shipbuilding requires high levels of skill and expertise to ensure that durable and seaworthy vessels are produced.
This demanding task involves working with various materials and techniques to achieve a secure and long-lasting bond. Welding also plays a crucial role in the repair and maintenance of ships, ensuring that they withstand the harsh conditions of the sea.
The use of modern technology and advanced welding methods has further improved the efficiency and quality of shipbuilding in Australia. With its significant contribution to the maritime industry, welding continues to be a critical component in the construction of safe and reliable vessels in Australia.
As the demand for ships continues to grow, the role of welding in shipbuilding will remain essential for the country’s maritime sector to thrive.
Overview of Australian shipbuilding industry
Growth and significance
- The Australian shipbuilding industry has experienced significant growth in recent years.
- It plays a vital role in supporting the country’s defense and maritime capabilities.
- This industry contributes to Australia’s economy by generating employment and fostering technological advancements.
- The growth of the industry has also led to increased investments and innovation in shipbuilding infrastructure.
- With the expansion of Australian naval fleet, the shipbuilding industry holds a strategic significance.
- Shipbuilding projects have seen a rise in demand due to increased trade and marine exploration activities.
- The industry’s growth has attracted skilled talent and expertise in ship design, engineering, and construction.
- Australia aims to be a global player in shipbuilding, strengthening its manufacturing capabilities.
- Government initiatives support the growth of the industry through policies and funding for research and development.
Key players and major projects
- Naval Group Australia is one of the leading players in Australian shipbuilding.
- The company is responsible for the construction of Attack-class submarines, a major defense project.
- BAE Systems Australia is actively involved in naval shipbuilding, including the Hunter-class frigates.
- These frigates will enhance Australia’s maritime power and provide advanced defense capabilities.
- ASC Shipbuilding, a subsidiary of BAE Systems, focuses on building Arafura-class offshore patrol vessels.
- This project aims to strengthen the country’s border protection and maritime security.
- Forgacs Marine and Defence specializes in constructing large commercial and defense vessels.
- They have contributed to significant projects such as Navy Supply Ships and Air Warfare Destroyers.
- Other notable players in the industry include Austal, Thales Australia, and Luerssen Australia.
- These companies have undertaken various shipbuilding projects, catering to diverse requirements.
The Australian shipbuilding industry’s growth and significance are evident in its expanding capabilities and contribution to national defense, economy, and technological advancement.
Key players in the industry, including Naval Group Australia, BAE Systems Australia, and ASC Shipbuilding, are involved in major projects that enhance maritime power and security.
With a supportive government framework and a pool of skilled talent, Australia aims to become a prominent global player in shipbuilding.
The industry’s continuous growth is driven by increasing demand, both domestic and international, for technologically advanced vessels.
This growth presents numerous opportunities for innovation, research and development, employment generation, and further investments in shipbuilding infrastructure.
By leveraging its strengths, Australia is poised to strengthen its position in the global shipbuilding market and bolster its maritime capabilities.+
Understanding welding in shipbuilding
Definition and purpose of welding
Welding is a process of joining metals together by melting and fusing them. Its purpose is to create a permanent and strong bond between metal components.
Types of welding techniques used in shipbuilding
- Gas metal arc welding (GMAW): Also known as MIG welding, it uses a continuous wire electrode and an inert gas to protect the weld.
- Shielded metal arc welding (SMAW): Commonly known as stick welding, it uses an electrode coated in flux to shield the weld from impurities.
- Flux-cored arc welding (FCAW): Similar to GMAW, but with a hollow wire filled with flux, providing better protection against impurities.
- Gas tungsten arc welding (GTAW): Also called TIG welding, it uses a tungsten electrode and an inert gas to produce a high-quality weld.
- Other specialized techniques: Shipbuilding may also involve underwater welding, friction stir welding, and laser beam welding.
Importance of welding in ship construction and maintenance
Welding plays a crucial role in shipbuilding as it ensures the structural integrity and safety of vessels. Here’s why
- Strength and durability: Welding creates strong and reliable joints that can withstand the harsh conditions at sea.
- Structural stability: Welding connects various sections and components of the ship, providing stability and structural integrity.
- Leak-proof sealing: Welding is used to join metal plates and pipes, creating leak-proof seals for fuel and water systems.
- Repair and maintenance: Welding enables the repair and maintenance of ships, extending their lifespan and improving their performance.
- Certification requirements: Welding in shipbuilding must adhere to strict industry standards and certifications to ensure safety and compliance.
In general, welding is an essential process in Australian shipbuilding. It involves various techniques such as gas metal arc welding, shielded metal arc welding, flux-cored arc welding, gas tungsten arc welding, and other specialized methods.
Welding is crucial for ship construction and maintenance, providing strength, durability, structural stability, leak-proof sealing, and allowing for repairs and maintenance.
The importance of welding in shipbuilding cannot be understated, as it ensures the safety and longevity of vessels operating in challenging marine environments.
Read: Top Plumbing Trends in Australian Engineering
Challenges and Demands of Welding in Australian Shipbuilding
High Standards and Certifications
- Australian shipbuilding industry requires welders to meet rigorous standards and obtain certifications.
- Welders must comply with international welding codes, such as the American Welding Society (AWS) or International Institute of Welding (IIW) standards.
- These high standards ensure the quality and structural integrity of the ships being built.
- Obtaining certifications can be challenging and time-consuming, requiring continuous education and skill improvement.
- Welders are responsible for maintaining their certification status, which includes regular recertification exams and assessments.
Understanding Complex Ship Designs
- Welders in Australian shipbuilding must possess a deep understanding of complex ship design blueprints.
- They need to interpret and comprehend various structural elements, including bulkheads, hulls, decks, and compartments.
- Accurate interpretation is crucial to ensure effective welding and adherence to safety and design specifications.
- Welders must collaborate closely with naval architects, engineers, and designers to comprehend the design intent and requirements.
- Continuous learning and staying updated on emerging shipbuilding technologies are essential for welders in this industry.
Safety Considerations and Regulations
- Safety is of utmost importance in Australian shipbuilding, and welders need to strictly adhere to safety protocols and regulations.
- Welders are exposed to hazardous materials, intense heat, and potentially dangerous environments.
- They must wear appropriate personal protective equipment (PPE) to minimize risks and ensure their own well-being.
- Welders also play a critical role in maintaining a safe work environment for their colleagues.
- Compliance with occupational health and safety regulations is essential to prevent accidents and injuries.
Work Environment and Various Conditions
- Welders in Australian shipbuilding work in diverse environments, including tight spaces, heights, and confined compartments.
- They face challenges like limited visibility, restricted access, and working at awkward angles.
- Adapting to different work conditions and maintaining welding quality requires exceptional skills and flexibility.
- Welders often work outdoors, facing harsh weather conditions like extreme temperatures, strong winds, and heavy rain.
- Despite these challenges, welders play a crucial role in constructing robust and seaworthy ships for Australia’s naval and commercial fleet.
Generally, welding in Australian shipbuilding comes with significant challenges and demands. Welders must meet high standards and obtain certifications to ensure the quality and integrity of the ships being built.
They need to understand complex ship designs and collaborate closely with other professionals in the industry. Safety considerations and adherence to regulations are paramount in this hazardous work environment.
Welders also face various conditions and must adapt their skills accordingly. Despite these difficulties, Australian shipbuilding relies on skilled welders to construct vessels that meet the nation’s maritime needs.
Read: The Future of Plumbing Tech in Australia
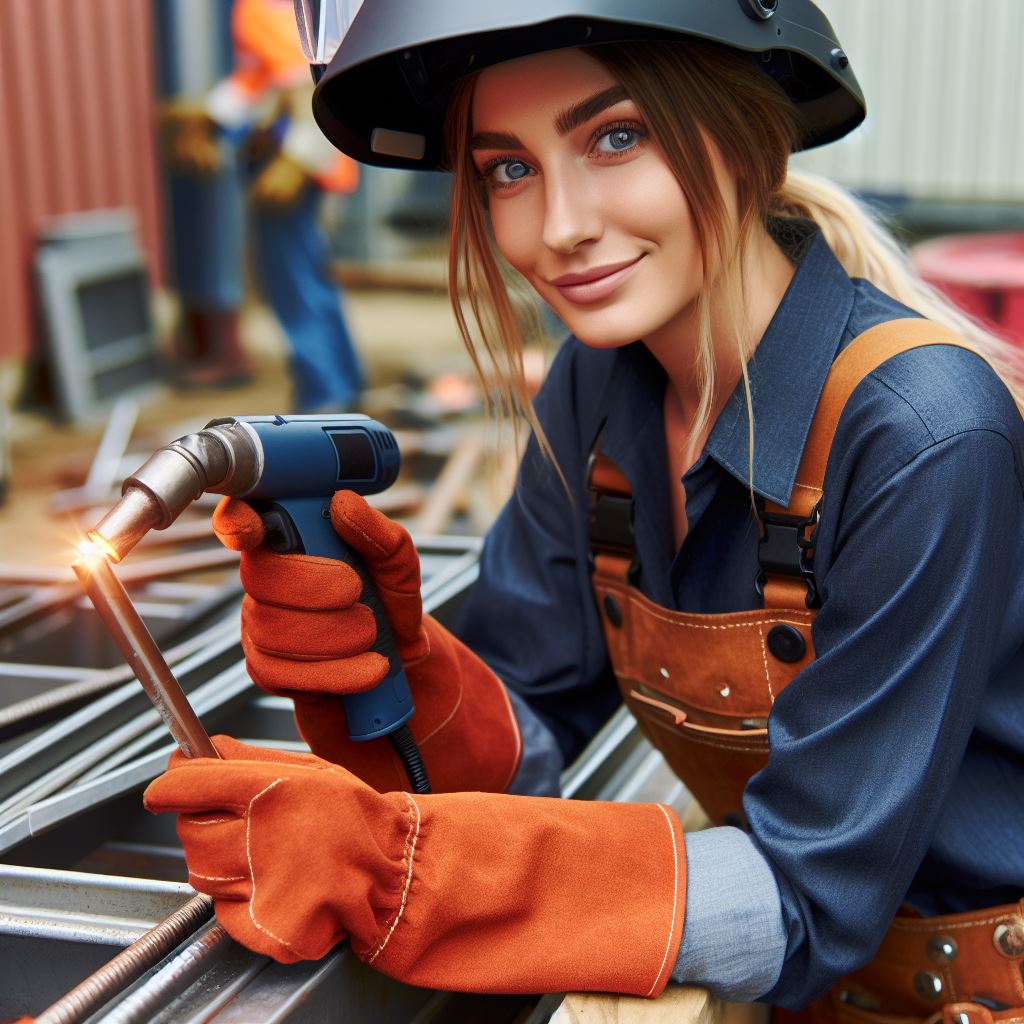
Gain More Insights: Safety Standards for Aussie Construction Sites
Skills and Qualifications Required for Welding in Shipbuilding
Formal Education, Training, and Certifications
- Completion of a formal education program in welding provides foundational knowledge and skills.
- Obtaining a certification, such as the Australian Welding Certification (AWC), further validates expertise.
- Essential training includes courses on welding techniques, safety protocols, and industry regulations.
- Continual professional development and staying updated with the latest advancements are crucial.
Experience and Practical Knowledge
- Gaining hands-on experience through apprenticeships or on-the-job training is invaluable.
- Practical knowledge of different welding methods, equipment, and materials is essential.
- Understanding the principles of metallurgy and how it applies to welding is crucial.
- Welders must possess the ability to interpret technical drawings and blueprints accurately.
Familiarity with Industry-Specific Requirements and Standards
- Having knowledge of industry-specific welding codes and standards is necessary.
- Shipbuilding requires compliance with international standards, such as ISO 3834 and AWS D3.6.
- Being well-versed in the classification societies’ rules and regulations ensures quality and safety.
- Familiarity with shipyard procedures, processes, and specific shipbuilding requirements is essential.
Welding in shipbuilding demands a range of skills and qualifications to perform tasks effectively. Let’s explore them:
Formal Education, Training, and Certifications
To begin a career in welding, individuals often pursue formal education programs focused on welding. These programs provide comprehensive theoretical knowledge and practical training.
Completion of a formal education program is an excellent foundation for a welding career. However, it’s important to supplement it with certifications to enhance credibility and demonstrate expertise.
One such certification widely recognized in Australia is the Australian Welding Certification (AWC). Achieving AWC allows welders to showcase their skills and abilities, increasing employability in the shipbuilding industry.
Furthermore, pursuing additional training courses specific to shipbuilding welding techniques, safety protocols, and industry regulations is paramount.
Continuous professional development ensures staying current with new welding methodologies and advancements in the field.
Experience and Practical Knowledge
While formal education and certifications provide a solid foundation, practical experience plays a crucial role in welding proficiency. Apprenticeships and on-the-job training opportunities allow welders to develop hands-on skills.
Your Personalized Career Strategy
Unlock your potential with tailored career consulting. Get clear, actionable steps designed for your success. Start now!
Get StartedWelders must develop practical knowledge of various welding methods and be proficient in using different welding equipment, tools, and materials.
Understanding the properties of different metals and their behavior during welding is essential for successful outcomes.
Additionally, welders must possess the ability to interpret technical drawings, blueprints, and welding symbols accurately. This ensures the ability to comprehend project requirements and execute welds accordingly.
Familiarity with Industry-Specific Requirements and Standards
Beyond technical skills, welders in shipbuilding must have a strong understanding of industry-specific requirements and standards.
Adhering to welding codes and standards is vital to ensure the structural integrity and safety of ships. Welders must familiarize themselves with internationally recognized standards such as ISO 3834 and AWS D3.6.
Moreover, shipbuilding involves compliance with classification societies’ rules and regulations, such as those by the Australian Maritime Safety Authority (AMSA) or the International Association of Classification Societies (IACS).
These organizations set guidelines to ensure the quality and safety of ship construction.
In addition to welding-related regulations, welders must have a comprehensive understanding of shipyard procedures, processes, and shipbuilding-specific requirements.
This knowledge enables them to adapt their welding techniques and practices to ensure optimal results in the shipbuilding industry.
In review, welding in shipbuilding requires a combination of formal education, training, practical experience, and industry-specific knowledge.
Welders who possess the necessary skills and qualifications can contribute to the successful construction and maintenance of ships in Australia.
Read: How to Become a Plumber in Australia
Learn More: Carpenter’s Salary in Australia: A Review
Job prospects and career opportunities in welding for shipbuilding
The shipbuilding sector currently has a high demand for skilled welders who can meet industry standards.
The shipbuilding industry in Australia is expected to witness significant growth and upcoming projects in the near future.
Welders in the shipbuilding sector can expect competitive salary ranges and attractive benefits packages.
There are ample advancement opportunities and various career paths available for welders in Australian shipbuilding.
Current demand for welders in the shipbuilding sector
The shipbuilding industry in Australia is experiencing a strong demand for welders who possess the necessary skills and qualifications.
As the construction of new ships and the maintenance of existing ones continue, the need for skilled welders becomes imperative.
Stand Out with a Resume That Gets Results
Your career is worth more than a generic template. Let us craft a resume and cover letter that showcase your unique strengths and help you secure that dream job.
Get HiredThe demand for welders is driven by the constant need for welding repairs, modifications, and maintenance on ships. Skilled welders are required to ensure the structural integrity of vessels and to meet stringent safety standards.
Welders are in high demand not only in the shipbuilding sector but also in other related industries such as oil and gas, offshore platforms, and defense.
This provides welders with diverse job opportunities and the chance to work on challenging projects.
Potential growth and upcoming projects
The future of the shipbuilding industry in Australia looks promising, with several major projects lined up. The government’s plan to invest in naval shipbuilding will create numerous job opportunities for welders.
The Naval Shipbuilding Plan aims to construct a fleet of next-generation naval vessels, including submarines and frigates. These projects will require a significant workforce, including skilled welders, to ensure successful completion.
In addition to the naval shipbuilding projects, other sectors of the shipbuilding industry, such as commercial and recreational shipbuilding, are also expected to grow. This opens up new avenues for welders to explore and expand their careers.
Salary ranges and benefits
Welders in the shipbuilding sector can expect competitive salary packages. The salaries depend on factors such as experience, skills, and the complexity of the welding work involved.
Entry-level welders typically earn around $40,000 to $50,000 per year, and as they gain experience and expertise, their salaries can reach $80,000 or more annually.
Welders who specialize in niche areas or hold supervisory positions may earn even higher salaries.
Apart from competitive pay, welders in the shipbuilding sector often receive attractive benefits packages, including health insurance, retirement plans, and paid leave.
These benefits contribute to a well-rounded compensation package, making welding in shipbuilding an appealing career choice.
Advancement opportunities and career paths
Welders in the shipbuilding industry have ample opportunities for career advancement. With experience and additional qualifications, welders can progress to higher positions, such as welding inspector or supervisor.
High-performing welders can transition into specialized roles, focusing on areas such as underwater welding, robotic welding, or advanced welding techniques.
These specialized roles often command higher salaries and offer more diverse and challenging projects.
Welders who aspire to advance their careers can also pursue further education and training to become welding engineers or take on managerial positions. The shipbuilding sector offers numerous pathways for welders to grow professionally and reach their full potential.
Essentially, the shipbuilding sector in Australia presents exciting job prospects and career opportunities for welders.
With a high demand for skilled welders, potential growth in the industry, competitive salary ranges, attractive benefits, and various advancement opportunities, welding in shipbuilding is a rewarding and fulfilling career choice.
Read: A Day in the Life of an Aussie Plumber
Learn More: Innovative Building Materials in Australia
Transform Your LinkedIn for Maximum Impact
Elevate your professional brand with a LinkedIn profile that attracts recruiters, showcases your expertise, and maximizes opportunities. Stand out in your industry with a profile built for success.
Boost ProfileConclusion
Discover the indispensable significance of welding in the realm of Australian shipbuilding.
In this exploration, delve into the intricate techniques that shape maritime structures.
Witness how welding meets the rigorous demands of ship construction, ensuring seaworthy integrity.
Uncover the essential skills required to navigate the complexities of this dynamic field.
As we navigate this journey, it becomes evident that welding is not merely a process; it’s the cornerstone of maritime craftsmanship.
Australian shipbuilding relies on skilled welders to forge connections that withstand the relentless forces of the open sea.
Embrace the challenge and opportunity that welding in shipbuilding presents.
Propel your career by mastering the techniques demanded by this vital industry.
Join the ranks of skilled professionals shaping the future of Australian shipbuilding.
The waves of opportunity are vast, and the time to embark on this exciting career path is now!