Introduction
Construction sites are inherently dangerous places, making safety standards of utmost importance.
In Australia, the construction industry faces significant risks and challenges in maintaining these standards.
With countless hazards such as falls, electrical accidents, and machinery-related incidents, safety standards play a vital role in protecting workers and preventing accidents.
By implementing and adhering to these standards, construction sites can minimize the risk of injuries and fatalities.
In the Australian construction industry, safety standards are governed by various regulations and legislation.
However, the current situation reveals room for improvement.
Despite efforts to enforce safety measures, accidents continue to occur, disrupting projects and harming workers.
One contributing factor to the current state is the complexity of construction projects.
With numerous contractors, subcontractors, and suppliers involved, coordinating safety practices becomes challenging.
Tight project schedules and budget constraints can compromise safety standards.
Another challenge is the lack of awareness and training among workers.
Many employees lack sufficient education on safety protocols or neglect prioritizing their own well-being.
Language barriers and cultural differences can hinder effective communication and understanding of safety standards.
Ongoing efforts strive to enhance safety standards in the Australian construction industry by promoting education, providing clear guidelines, and fostering a safety-oriented culture.
These endeavors hold the potential for significant improvements.
In a nutshell, safety standards are crucial for construction sites in Australia.
The current situation highlights the need for greater attention to this aspect of the industry to ensure the well-being of workers and prevent accidents.
Efforts must continue to enhance safety regulations, awareness, and training to create a safer construction environment.
Regulatory Bodies and Legislation
The relevant regulatory bodies responsible for enforcing safety standards
- Safe Work Australia: The main body responsible for developing and implementing national policy and standards.
- State and Territory Regulators: Each state has its own regulatory body for enforcing safety standards.
- Construction, Forestry, Maritime, Mining, and Energy Union (CFMMEU): An influential labor union involved in promoting safety on construction sites.
Overview of the legislation and regulations in place to ensure safety on construction sites
- Work Health and Safety Act 2011: An essential legislation that sets out the framework for ensuring health and safety in workplaces.
- Construction Work Code of Practice: Provides guidance on managing risks specific to the construction industry.
- Electrical Safety Act 2002: Focuses on electrical safety to prevent accidents and ensure compliance with standards.
- Building Code of Australia: Includes provisions related to safety, accessibility, fire safety, and structural integrity.
- Australian Standards: Various standards, such as AS/NZS 4801 for safety management systems, guide safety practices on construction sites.
- Personal Protective Equipment (PPE) Regulations: Mandate the use of appropriate PPE to protect workers from potential hazards.
- Noise Regulations: Set limits on acceptable noise levels in construction areas to protect workers and nearby residents.
- Hazardous Substances and Dangerous Goods Regulations: Regulate the handling, storage, and transportation of hazardous materials on construction sites.
The role of regulatory bodies and legislation in ensuring safety on construction sites
- Setting standards: Regulatory bodies develop and update safety standards to prevent accidents and promote a safe working environment.
- Enforcing compliance: Inspections and audits are conducted to ensure construction sites adhere to the prescribed regulations.
- Investigating incidents: Regulatory bodies investigate accidents and incidents to identify causes, improve safety measures, and hold responsible parties accountable.
- Providing guidance and resources: Regulatory bodies issue guidelines and resources to assist companies in implementing safety practices and complying with regulations.
- Promoting education and training: Training programs and campaigns are organized to create awareness and improve knowledge of safety standards among workers.
Benefits of strict safety standards on construction sites
- Minimizing accidents and injuries: Proper safety measures reduce the risk of accidents and ensure the well-being of workers and the public.
- Improving productivity: When workers feel safe, they can focus on their tasks, which increases productivity and efficiency.
- Cost savings: Avoiding accidents and injuries reduces medical costs, insurance premiums, and potential legal liabilities for construction companies.
- Enhancing reputation: Adhering to strict safety standards demonstrates a commitment to worker welfare and improves the company’s reputation.
- Fostering a positive work culture: Prioritizing safety creates a culture of care, trust, and respect among workers, leading to higher job satisfaction.
In essence, regulatory bodies and legislation play a crucial role in maintaining safety standards on Australian construction sites.
By setting standards, enforcing compliance, providing guidance, and promoting education, these bodies ensure the well-being of workers and the success of the construction industry as a whole.
Strict safety standards not only prevent accidents and injuries but also enhance productivity, save costs, and improve a company’s reputation.
Key Safety Standards
- Construction sites must adhere to essential safety standards to ensure worker protection.
- These standards encompass various aspects including personal protective equipment (PPE), fall protection, and hazard communication.
Personal Protective Equipment (PPE)
- PPE is crucial for construction workers to minimize exposure to potential hazards.
- Equipment such as hard hats, safety glasses, gloves, and safety shoes must be worn at all times.
- Workers should also use respiratory protection, earplugs, and reflective vests when necessary.
- Regular inspection and maintenance of PPE should be conducted to ensure effectiveness.
Fall Protection
- Construction sites must implement fall protection measures to prevent falls from elevated areas.
- Guardrails, safety nets, and personal fall arrest systems (PFAS) should be utilized appropriately.
- Workers should receive proper training on fall protection systems and their usage.
- Regular inspections of fall protection equipment are necessary to identify any potential issues.
Hazard Communication
- Effective communication of hazards is critical for construction site safety.
- All hazardous chemicals must be properly labeled, providing necessary information and warnings.
- Workers should receive training on how to handle hazardous materials and understand safety data sheets (SDS).
- Regular safety meetings should be conducted to ensure workers are informed about potential hazards.
Excavation and Trenching Safety
- Construction sites involving excavation and trenching operations need specific safety measures.
- Workers should be trained to identify potential hazards like cave-ins and implement protective systems.
- Regular inspections of excavation areas are crucial to detect any unstable soil conditions.
- Access and egress points should be properly maintained to ensure safe entry and exit.
Electrical Safety
- Proper electrical safety practices are necessary to prevent incidents on construction sites.
- Regularly inspect and maintain electrical equipment to prevent malfunctions.
- Train workers to identify electrical hazards and follow lockout/tagout procedures.
- Use ground fault circuit interrupters (GFCIs) for protection against electric shock hazards.
Fire Safety
- Construction sites must have effective fire safety measures to protect workers and property.
- A comprehensive fire prevention plan should be in place, including fire extinguishers and emergency exits.
- Conduct frequent fire drills to familiarize workers with evacuation procedures, ensuring their preparedness.
- Properly store and handle flammable materials to minimize fire risks.
Adhering to safety standards is fundamental in ensuring the protection of workers on Australian construction sites.
By implementing the necessary measures related to personal protective equipment, fall protection, hazard communication, and other areas, construction sites can create a safe working environment for all employees.
Training and Certification Requirements
To uphold safety standards on Aussie construction sites, workers must undergo specific training and certification. This section outlines requirements, certifications, and their relevance.
- Construction site workers in Australia must actively undergo specific training to meet and uphold safety standards.
- This training helps workers understand and implement safety procedures, preventing accidents and injuries.
- One of the key certifications in the construction industry is the Construction White Card.
- The Construction White Card is mandatory for individuals wishing to work in construction in Australia.
- It ensures that workers have a basic understanding of safety practices and regulations on construction sites.
- Another important certification is the Occupational Health and Safety (OHS) Certificate.
- The OHS Certificate focuses on identifying and managing workplace hazards to ensure a safe working environment.
- Workers with this certification possess in-depth knowledge of safety procedures and risk assessment.
- For specialized roles, additional certifications may be required, such as Working at Heights Certification.
- This certification is necessary for workers who will be working at elevated heights, like on scaffolding or roofs.
Different Certifications and their Relevance
- Construction White Card: This certification is essential for all construction workers, ensuring a basic understanding of safety.
- OHS Certificate: This certification is crucial for individuals involved in managing safety and dealing with workplace hazards.
- Working at Heights Certification: This certification is necessary for workers in elevated positions to reduce fall-related accidents.
- Confined Space Entry Certification: Workers in confined spaces, like tanks or tunnels, need this certification to safely perform their tasks.
- Forklift License: This license is required for workers operating forklifts on construction sites, ensuring their competency.
- Dangerous Goods License: Workers handling or transporting hazardous materials must have this license to prevent accidents.
- Electrical Safety Certification: Electrical workers need this certification to safely handle electrical installations and components.
- First Aid and CPR Certification: Workers trained in first aid and CPR can provide immediate assistance in case of accidents or injuries.
- Asbestos Removal Certification: This certification is crucial for workers involved in asbestos removal to prevent exposure and health risks.
- Fire Safety Certification: Workers trained in fire safety can effectively respond to fires and ensure the safety of everyone on site.
Complying with safety standards on construction sites is of utmost importance to protect the well-being of workers and prevent accidents.
Workers enhance knowledge and skills through designed training and certification, empowering them to identify and mitigate potential risks.
Employers should ensure that their workers receive the necessary training and certifications to create a safe work environment.
Read: A Day in the Life of an Aussie Plumber
Safety Inspections and Audits
Construction sites conduct safety inspections and audits actively to ensure compliance with safety standards.
Process of Safety Inspections and Audits
- Inspections and audits involve a thorough examination of the construction site to identify potential hazards.
- Inspectors assess the implementation of safety protocols, equipment maintenance, and adherence to regulatory requirements.
- Evidence is collected, such as photographs and documentation, to support findings during inspections.
- Audit reports are prepared after evaluations that outline non-compliance issues and corrective actions required.
- Corrective actions may involve training programs, equipment upgrades, or modifications to improve safety measures.
- Follow-up inspections are conducted to monitor the effectiveness of corrective actions implemented.
Authorities Conducting Inspections and Audit Frequency
- The responsibility for safety inspections lies with various authorities, depending on the jurisdiction.
- In Australia, occupational health and safety regulators and government agencies are involved in inspections.
- Safework Australia is a federal body responsible for developing and promoting national WHS policies.
- Additionally, state-based regulators, such as WorkSafe Victoria and WorkCover NSW, conduct inspections.
- The frequency of inspections and audits varies depending on the level of risk associated with construction activities.
- High-risk construction sites may face more frequent inspections, sometimes unannounced, to ensure ongoing compliance.
- Regular inspections occur during different stages of construction, including pre-construction, ongoing work, and project completion.
Safety inspections and audits actively uphold construction site safety by assessing, collecting evidence, and addressing non-compliance promptly.
Occupational health and safety regulators, along with government agencies, are responsible for conducting inspections and audits.
The frequency of these inspections varies depending on the level of risk associated with construction activities.
By adhering to safety standards and addressing any identified issues promptly, construction sites can ensure the well-being of workers and minimize potential accidents or hazards.
Read: Carpentry Apprenticeships: What to Expect
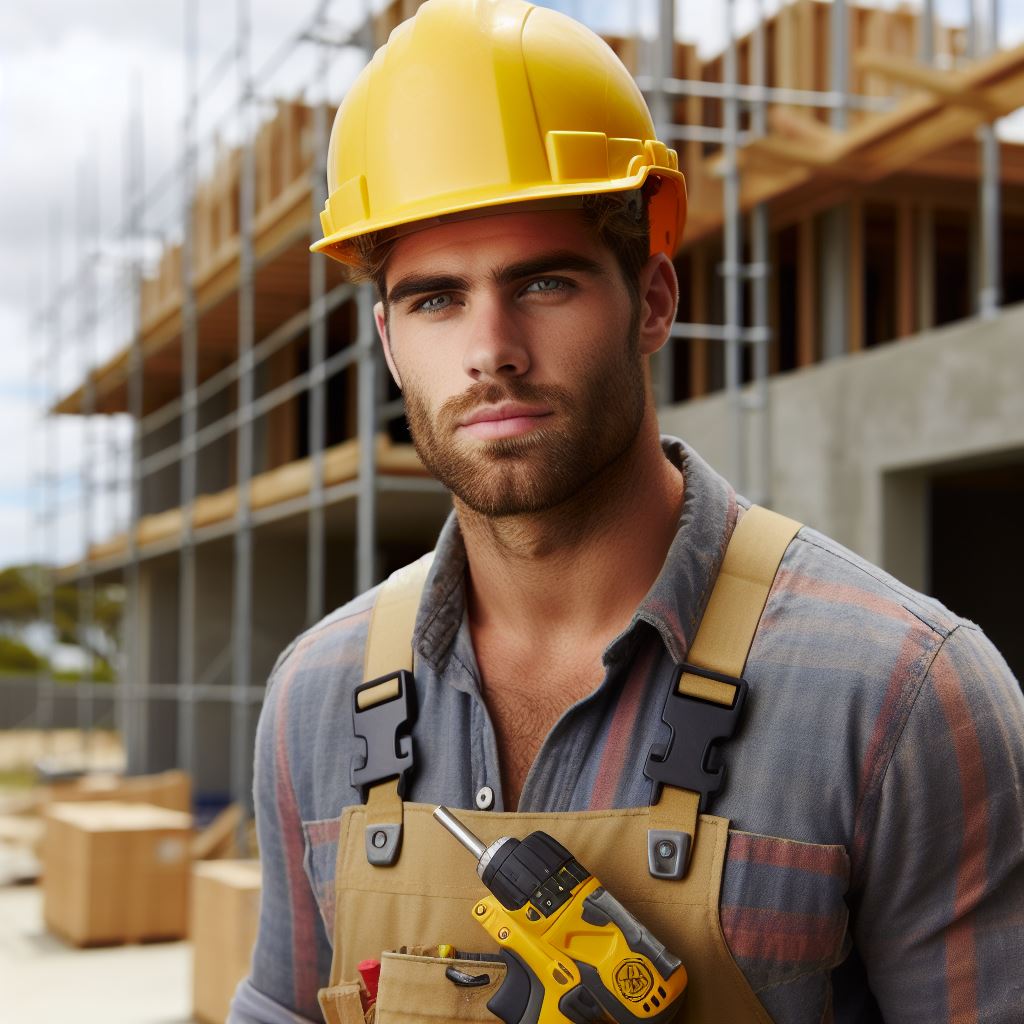
Gain More Insights: Welding in Australian Shipbuilding: A Focus
You Might Also Like: Aussie Mech Engineers in the Auto Industry
Uncover the Details: Women in Carpentry: Changing the Scene
Challenges and Issues
Common challenges and issues that hinder the implementation of safety standards
- Insufficient training and awareness among construction workers regarding safety protocols.
- Lack of proper supervision and monitoring on construction sites, leading to non-compliance.
- Inadequate communication and coordination between different stakeholders, causing confusion and negligence.
- Failure to prioritize safety due to tight project deadlines and financial constraints.
- Resistance to change and reluctance to adopt new safety practices and technology.
- Inadequate enforcement of safety regulations by regulatory authorities and lack of penalties for non-compliance.
- High turnover rate in the construction industry, resulting in a constant need for training new workers.
The potential consequences of non-compliance
- Increase in accidents and injuries, putting the lives of construction workers at risk.
- Loss of productivity and delays in project completion due to accidents and legal investigations.
- Damages to the reputation of construction companies, leading to loss of clients and future opportunities.
- Legal consequences, including fines and penalties for non-compliance with safety standards.
- Physical and emotional trauma experienced by workers and their families.
- Rising insurance costs for construction companies due to frequent accidents and injuries.
- Negative impact on the overall morale and motivation of the workforce, leading to decreased productivity.
- Inability to attract and retain skilled workers due to a poor safety track record.
Despite challenges, the construction industry must prioritize safety.
Effective measures reduce accidents.
Construction companies should invest in comprehensive worker training, ensuring safety awareness and risk mitigation skills.
Regular supervision ensures safety compliance.
Clear communication among stakeholders promotes coordination, minimizing confusion.
Prioritizing safety is not just ethical; it’s a smart business decision. Compliance helps avoid legal actions and reputation damage.
Construction companies must recognize safety as a business imperative. Implementing standards prevents costly consequences.
Regulatory authorities play a vital role.
They should enforce strict regulations, imposing penalties for non-compliance to deter irresponsible practices.
Overcoming safety challenges is crucial for worker well-being and project success.
Addressing challenges and understanding consequences creates a safer, sustainable working environment in Australian construction.
Your Personalized Career Strategy
Unlock your potential with tailored career consulting. Get clear, actionable steps designed for your success. Start now!
Get StartedRead: Challenges Facing Aussie Plumbers Today
Uncover the Details: Australian Welding Standards & Compliance
Best Practices and Case Studies
Australia’s construction sites rigorously follow safety standards to protect workers and prevent accidents causing injuries or fatalities.
In this section, we will highlight successful examples of construction sites with exemplary safety standards and share best practices that other construction sites can adopt to improve safety.
Successful Examples of Construction Sites with Exemplary Safety Standards
Sydney Opera House Construction Site
- Implemented a comprehensive safety management system to ensure the safety of workers and visitors.
- Conducted regular safety training programs for all employees to create awareness and promote safe practices.
- Implemented strict protocols for working at heights and handling heavy machinery, reducing the risk of accidents.
Melbourne Metro Tunnel Project
- Adopted a proactive approach towards safety by conducting site inspections and risk assessments regularly.
- Encouraged open communication among workers to report near misses, hazards, and safety concerns promptly.
- Implemented a safety rewards program to recognize and incentivize employees who actively contributed to maintaining a safe work environment.
Brisbane Skytower Construction Site
- Strictly enforced the use of personal protective equipment (PPE) for all workers, including hard hats, safety boots, and high-visibility clothing.
- Conducted regular toolbox talks to educate workers about potential hazards, emergency procedures, and safe work practices.
- Implemented a robust incident reporting system to ensure timely investigation and resolution of safety incidents.
Best Practices for Improving Safety Standards
Comprehensive Safety Training
- Provide thorough safety training to all employees, including new hires, to ensure they are aware of potential hazards and know how to mitigate them.
- Conduct regular refresher courses to reinforce safe work practices and address new safety concerns.
Risk Assessment and Hazard Identification
- Conduct regular risk assessments to identify potential hazards and take necessary measures to eliminate or control them.
- Implement a hazard reporting system where workers can report unsafe conditions or near misses, encouraging a proactive safety culture.
Clear Communication and Collaboration
- Encourage workers and supervisors to openly communicate, fostering an environment where they freely address and resolve safety concerns.
- Encourage collaboration between different construction teams to ensure seamless coordination and adherence to safety protocols.
Regular Inspections and Audits
- Conduct regular inspections to identify any deviations from safety standards and take immediate corrective actions.
- Perform audits to assess the effectiveness of safety measures and identify areas for improvement.
Continuous Improvement
- Regularly review and update safety policies and procedures to align with changing regulations and industry best practices.
- Encourage a culture of continuous improvement by actively seeking feedback from workers and implementing their suggestions for enhancing safety.
By highlighting successful examples and sharing best practices, construction sites across Australia can strive for exemplary safety standards.
Adopting these practices will not only ensure the well-being of workers but also enhance productivity, reduce downtime, and establish a positive reputation for the construction industry as a whole. Remember, a safe construction site is a productive construction site.
Read: Carpentry 101: An Aussie’s Guide to the Trade
Delve into the Subject: Mechanical Engineering Internships in Oz
Conclusion
Safety standards for Australian construction sites are of utmost importance to protect workers and minimize accidents and fatalities.
Compliance with these standards needs to be prioritized by the industry as a whole.
It is crucial for all stakeholders, including contractors, workers, and regulatory bodies, to actively promote and enforce safety practices on construction sites.
This can be achieved through regular training, inspections, and the creation of a culture that values safety above all else.
Implementing safety measures is cost-effective, preventing severe consequences. Demonstrating a commitment to safety enhances the construction industry’s reputation and credibility.
Safety standards play a critical role in safeguarding the lives and well-being of workers on Australian construction sites.
It is essential that the industry embraces these standards and works collectively to create a safe and secure work environment for everyone involved.