Introduction
Welding is the process of joining separate metal pieces through heating and melting. It plays a crucial role in Australian industry, as it enables the creation of strong and durable structures.
Brief Explanation of Welding
Welding involves the application of heat to melt the base metals, which later solidify and create a strong bond. It is an intricate process that requires skill and precision.
Importance of Welding in Australian Industry
Welding is vital in Australian industry as it allows the construction of buildings, bridges, and infrastructure. Manufacturing industries employ it actively to fabricate products and components efficiently.
Additionally, welding ensures the safety and reliability of structures by providing secure connections. It enhances the longevity of materials and helps maintain the integrity and functionality of industrial equipment.
Various Welding Techniques Used in Australian Industry
- Gas Metal Arc Welding (GMAW): It uses a wire electrode and a shielding gas to create high-quality welds swiftly.
- Shielded Metal Arc Welding (SMAW): Commonly known as stick welding, it uses a coated electrode and is versatile in various conditions.
- Flux-Cored Arc Welding (FCAW): Similar to GMAW, it uses a tubular electrode filled with flux, providing better weld penetration and higher deposition rates
- Gas Tungsten Arc Welding (GTAW): Known as TIG welding, it uses a non-consumable tungsten electrode and inert gas for precise and clean welds.
Welding is an essential process in Australian industry, enabling the fabrication of structures and the production of various products.
The right choice of welding technique ensures the strength, durability, and safety of materials and equipment used in different industries.
Shielded Metal Arc Welding (SMAW)
Brief explanation of SMAW
SMAW is a welding process that uses a consumable electrode covered by a flux to create an electric arc.
Application of SMAW in Australian industry
- SMAW dominates Australia’s construction, shipbuilding, pipeline, and structural steel industries due to its widespread use.
- It actively serves maintenance and repair tasks across diverse sectors.
Advantages and limitations of SMAW
Advantages
- Execute a versatile welding method in multiple positions, employing a simple yet effective technique.
- Perform outdoor welding on-site, making it suitable for on-site welding applications.
- Does not require a shielding gas, reducing costs
Limitations
- Welding generates slag requiring cleaning afterward.
- Lower welding speed compared to other techniques.
- Requires skilled welders due to the need for manual control.
Examples of industries that use SMAW in Australia
- Shipbuilders actively weld ship hulls, decks, and superstructures in the shipbuilding industry.
- Welders actively construct ship hulls, decks, and superstructures in the shipbuilding industry.
- Welders actively weld bridges, buildings, and various steel structures using structural steel.
- Welders use structural steel in actively welding bridges, buildings, and various steel structures.
- “SMAW plays a crucial role in the maintenance and repair industry, fixing diverse metal components effectively.”
Read: Plumbing 101: A Beginner’s Guide in Australia
Gas Metal Arc Welding (GMAW)
Gas Metal Arc Welding (GMAW) is a welding technique that uses a consumable electrode wire, inert gas, and an electrical power source to create a weld. MIG welding, also called Metal Inert Gas welding, employs an inert gas to melt and join metals.
Australian industries widely use GMAW for its versatile and efficient welding capabilities. It suits welding steel, stainless steel, and aluminum materials, ranging from thin to thick.
It is particularly suitable for welding thin to thick materials made of steel, stainless steel, and aluminum.
There are several advantages of using GMAW in welding
- High welding speed: GMAW allows for fast welding due to its continuous wire feed system and high heat input. This makes it ideal for high-volume production.
- Easy to learn and use: GMAW is relatively easy to learn compared to other welding techniques. It offers good control over the weld pool and produces clean and aesthetically pleasing welds.
- Less spatter and fumes: GMAW produces minimal spatter and fumes, reducing the need for post-weld cleaning and ensuring a healthier work environment.
- GMAW suits diverse industries, handling thin and thick materials effectively, demonstrating versatility in numerous applications.
However, GMAW also has a few limitations
- Limited outdoor use: GMAW requires the use of shielding gas to protect the weld from atmospheric contamination. This makes it less favorable for outdoor welding where wind can disrupt the shielding gas.
- GMAW equipment, comprising the power source, wire feeder, and gas cylinder, can outweigh costs in alternative welding methods.This might pose a financial challenge for small-scale operations.
There are numerous industries in Australia that rely on GMAW for their welding needs. Some notable examples include
- GMAW plays a crucial role in crafting vehicle components like frames, exhaust systems, and body panels in automotive manufacturing.
- GMAW actively shapes structural steel for buildings, bridges, and infrastructure projects in the construction industry.
- Aerospace industry: GMAW is utilized in the manufacturing and repair of aircraft components such as fuselages, wings, and engine parts.
- Mining industry: GMAW is crucial for the construction and maintenance of mining equipment, including conveyor systems, drills, and storage tanks.
- Manufacturing industry: GMAW is extensively employed in the production of metal products, such as appliances, furniture, and machinery parts.
Therefore, Gas Metal Arc Welding (GMAW) is a widely used welding technique in Australian industry, offering advantages such as high welding speed, ease of use, and versatility.
However, it also has limitations regarding outdoor use and equipment cost. GMAW finds applications in various industries, including automotive, construction, aerospace, mining, and manufacturing.
Read: The Future of Plumbing Tech in Australia
Flux-Cored Arc Welding (FCAW)
Brief explanation of FCAW
Flux-Cored Arc Welding (FCAW) is a welding process that uses a continuously fed electrode with a flux core.
Application of FCAW in Australian industry
FCAW is commonly used in Australian industries that require high-quality and efficient welding, such as construction and mining.
Advantages and limitations of FCAW
The advantages of FCAW include higher deposition rates, deep penetration, and the ability to weld in various positions.
However, it has limitations, such as increased fume generation and the need for proper ventilation.
Examples of industries that use FCAW in Australia
- Construction industry: FCAW is widely used for welding structural steel and repairing heavy machinery.
- Mining industry: FCAW is employed in fabricating and maintaining mining equipment and infrastructure.
- Oil and gas industry: FCAW is used for pipeline welding and structural fabrication in this sector.
Flux-Cored Arc Welding (FCAW) is a popular welding technique used in the Australian industry due to its numerous advantages. By understanding its application and limitations, we can appreciate its significance in various sectors.
Your Personalized Career Strategy
Unlock your potential with tailored career consulting. Get clear, actionable steps designed for your success. Start now!
Get StartedBrief explanation of FCAW
FCAW is a welding process that utilizes a continuously fed electrode with a flux core. This core produces a shielding gas, protecting the weld pool from contaminants.
The electrode, which contains a flux material, helps generate a protective gas shield and produces slag, which shields the weld as it cools. This characteristic makes FCAW suitable for outdoor use and can be performed in windy conditions.
Application of FCAW in Australian industry
FCAW finds wide applications in Australian industries that require high-quality and efficient welding. One such industry is construction, where FCAW is extensively used for welding structural steel in building frameworks.
Moreover, FCAW is also employed in the mining industry for fabricating and repairing heavy machinery, mining equipment, and infrastructure. Its ability to provide optimum weld quality and high deposition rates makes it ideal for these applications.
Advantages and limitations of FCAW
Advantages
- FCAW offers higher deposition rates compared to other welding processes, reducing overall welding time.
- It provides deep penetration, resulting in strong welds with good mechanical properties.
- FCAW can be performed in various positions, allowing flexibility in welding complex structures.
Limitations
- FCAW generates more fumes and requires proper ventilation to ensure a safe working environment.
- The weld quality may be affected by environmental factors, such as wind, due to the use of an external shielding gas.
Examples of industries that use FCAW in Australia
Construction industry
The construction industry extensively uses FCAW for welding structural steel in buildings, bridges, and infrastructure. FCAW provides high-quality welds with good penetration, ensuring the integrity and safety of these structures.
Mining industry
In the mining sector, FCAW plays a vital role in fabricating and maintaining mining equipment and infrastructure. The ability of FCAW to weld heavy materials and its high deposition rates make it suitable for the demanding conditions in mines.
Oil and gas industry
The oil and gas industry often utilizes FCAW for pipeline welding, as it can provide high-quality welds that meet the rigorous industry standards.FCAW actively fabricates platforms, rigs, and crucial components in structural manufacturing for various applications.
Flux-Cored Arc Welding (FCAW) has become an essential welding technique in Australian industries.
Its versatility, high deposition rates, and ability to withstand demanding environments make it a preferred choice for various applications, from construction to mining and oil and gas sectors.
Read: A Day in the Life of an Aussie Plumber
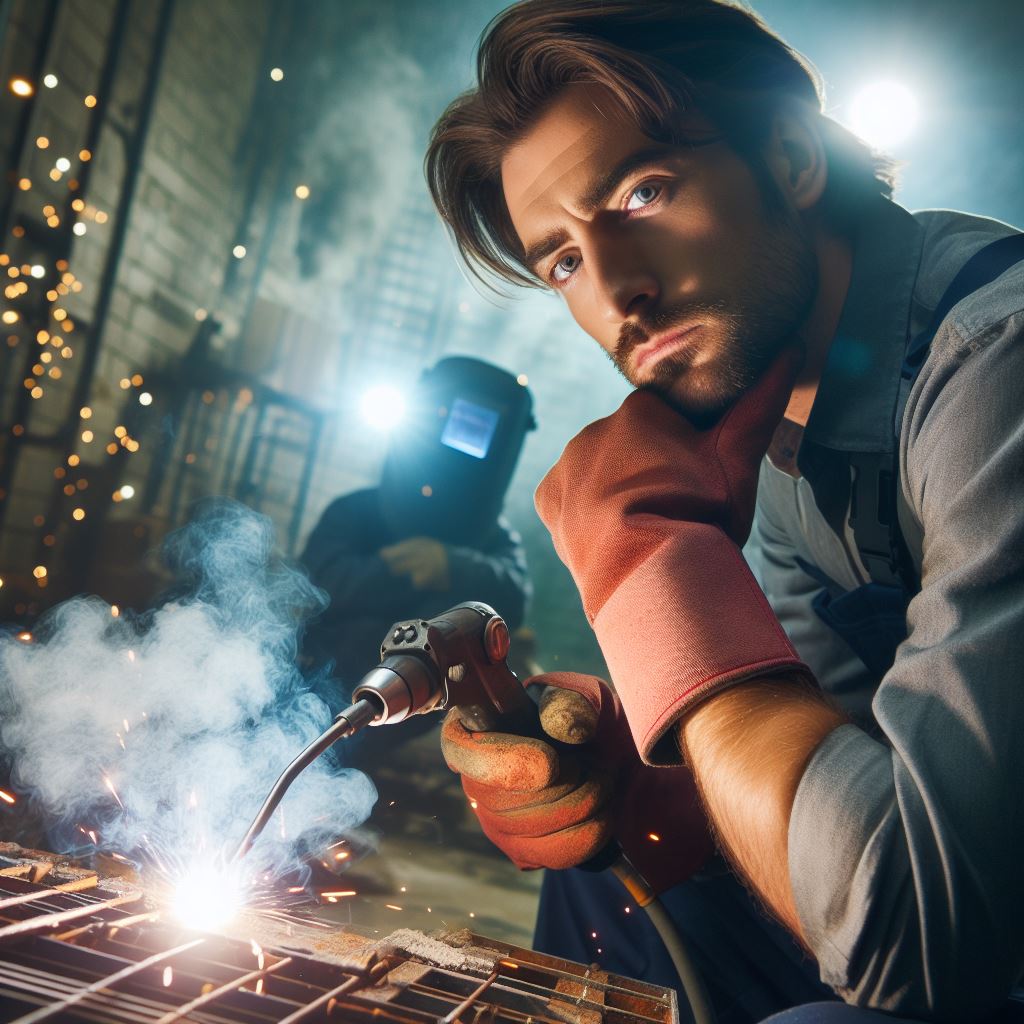
Tungsten Inert Gas Welding (TIG)
Brief explanation of TIG welding
- TIG welding, also known as Gas Tungsten Arc Welding (GTAW), uses a non-consumable tungsten electrode to create the weld.
- Argon shields the weld area from atmospheric contamination, providing protection against external elements during the welding process.
- The process allows for precise control over the heat input and produces high-quality, clean welds.
Application of TIG welding in Australian industry
- TIG welding, known for its versatility, welds materials like stainless steel, aluminum, and copper alloys widely in the Australian industry.
- It is commonly used in the fabrication of pressure vessels, aerospace components, and automotive parts.
- The precision and control offered by TIG welding make it suitable for applications that require aesthetic appeal and critical joint integrity.
Advantages and limitations of TIG welding
Advantages
- TIG welding produces high-quality welds with excellent visual appearance and minimal distortion.
- The process allows for precise control over the weld, resulting in accurate and consistent results.
- It can be used to weld a wide range of materials and thicknesses.
- TIG welds have good mechanical properties, high strength, and resistance to corrosion.
Limitations
- TIG welding is a slower process compared to other welding techniques, which can affect productivity.
- It requires a higher skill level from the welder due to the need for manual control and coordination.
- The process is less suitable for thick sections or materials with poor thermal conductivity.
- It is generally more expensive than other welding methods due to the equipment and labor costs.
Examples of industries that use TIG welding in Australia
Aerospace Industry
- TIG welding forms aircraft components like fuselages, engine parts, and fuel tanks with precision in manufacturing.
- The high-quality welds produced by TIG welding ensure the integrity and safety of these critical components.
Automotive Industry
- TIG welding shapes exhaust systems, chassis, and roll cages in production commonly.
- The aesthetic appeal and strength of TIG welds make them suitable for high-performance vehicles.
Pharmaceutical Industry
- TIG welding fabricates stainless steel equipment for pharmaceutical manufacturing, ensuring precision and quality in the process.
- The clean and contamination-free welds make TIG welding suitable for maintaining hygienic conditions.
Food and Beverage Industry
- TIG welding constructs stainless steel tanks, pipelines, and processing equipment in the construction industry.
- The sanitary welds produced by TIG welding meet the stringent hygiene requirements of this industry.
TIG welding has become an integral part of the Australian industry due to its versatility and ability to produce high-quality welds.
Despite limitations, it suits aerospace, automotive, pharmaceutical, and food industries due to its precision and control.
Read: How to Become a Plumber in Australia
Conclusion
Recap of the top welding techniques used in Australian industry
In this section, we have discussed the top welding techniques commonly used in Australian industry. These include Tungsten Inert Gas (TIG) welding, Metal Inert Gas (MIG) welding, and Shielded Metal Arc Welding (SMAW).
Each technique has its strengths and advantages in different applications.
Importance of understanding different welding techniques
It is crucial for welders and those aspiring to enter the welding industry to have a comprehensive understanding of these techniques.
This knowledge allows for the selection of the most suitable method for each job, resulting in high-quality and durable welds.
Explore welding in Australia—unlock growth, specialize, and advance. Overcome challenges, embrace rewards. Fulfilling career awaits with creativity, stability, and potential.
With the increasing demand for skilled welders in Australia, exploring welding as a career path can lead to fulfilling and financially rewarding opportunities.
Taking the time to develop expertise in various welding techniques opens doors to job prospects in various industries, including construction, manufacturing, and automotive.
Stand Out with a Resume That Gets Results
Your career is worth more than a generic template. Let us craft a resume and cover letter that showcase your unique strengths and help you secure that dream job.
Get Hired“Familiarize yourself with top welding techniques in Australian industry. Pursue further education for an exciting and promising welding career in Australia.”
Don’t hesitate to dive deeper into this field and make a valuable contribution to the nation’s industrial landscape.