Introduction
Welding plays a crucial role in multiple industries by joining materials together securely.
Now, let’s delve into the role of robotics in Australian welding and its significance.
Importance of welding in various industries
Welding has become an essential process in various industries, as it enables the joining of materials together securely, creating robust structures. From construction to manufacturing, welding ensures the durability and integrity of products.
However, traditional welding techniques involve human labor, which can be time-consuming, costly, and even dangerous.
In recent years, the Australian welding industry has witnessed a significant shift towards automation and the adoption of robotics. Robotic welding systems have revolutionized the welding process by enhancing efficiency, accuracy, and safety.
These robotic systems are equipped with advanced sensors and precise control mechanisms, enabling them to perform welds with optimal precision.
Role of robotics in Australian welding
The use of robots in welding has enabled industries to achieve higher production rates and consistent quality.
The automated nature of these systems ensures uniformity in welds, eliminating errors and rework. Moreover, robots can work continuously without breaks, reducing downtime and increasing productivity.
In Australian welding, the addition of robotics has also improved the working conditions for welders. Robots can handle hazardous and repetitive tasks, eliminating the risk of exposure to harmful fumes and reducing physical strain on workers. This has not only enhanced worker safety but also improved overall job satisfaction.
Furthermore, the integration of artificial intelligence (AI) in robotic welding has led to advanced capabilities, such as adaptive welding and real-time monitoring. AI algorithms allow robots to adapt to different welding scenarios, resulting in precise welds on a wide range of materials.
Real-time monitoring enables immediate detection of any defects or deviations, ensuring prompt corrective actions.
Basically, the role of robotics in Australian welding has transformed the industry by improving efficiency, quality, and safety. With the continuous advancements in technology, robotic welding systems will continue to play a significant role in shaping the future of welding in Australia.
In this section, we will provide a historical overview of welding in Australia, focusing on the evolution and advancements in traditional welding techniques. We will also explore the challenges faced by human welders in terms of productivity and safety.
Historical overview of welding in Australia
Evolution and advancements in traditional welding techniques
Welding has a long and rich history in Australia, dating back to the early 19th century. Initially, blacksmiths were primarily responsible for joining metals through various heating and hammering techniques.
As industrialization took hold, welding techniques began to evolve. The introduction of the oxy-acetylene welding process in the early 20th century revolutionized the industry. This technique allowed for higher temperatures, enabling the welding of various metals with greater precision and strength.
Over the years, traditional welding techniques continued to advance. The introduction of shielded metal arc welding (SMAW) in the 1920s allowed for more efficient and versatile metal joining. This technique became widely adopted in Australia, particularly in the construction and manufacturing sectors.
The 1950s witnessed another significant advancement with the introduction of gas metal arc welding (GMAW), also known as MIG welding. This process involved a continuously fed wire electrode, improving the speed and efficiency of welding. It quickly became the preferred technique for many industries.
By the 1980s, Australia saw further advancements in welding technology with the introduction of tungsten inert gas (TIG) welding. This process offered precise control over the welding arc, making it suitable for intricate and high-quality welds.
Challenges faced by human welders in terms of productivity and safety
Despite the advancements in traditional welding techniques, human welders faced several challenges that hindered productivity and safety.
Your Personalized Career Strategy
Unlock your potential with tailored career consulting. Get clear, actionable steps designed for your success. Start now!
Get StartedOne of the key challenges was the repetitive nature of welding work. Human welders often had to perform the same welds repeatedly, leading to fatigue and reduced productivity. This not only affected the overall efficiency of welding operations but also increased the risk of errors and accidents.
Additionally, welding poses several safety risks for human welders. Exposure to hazardous fumes, intense heat, and ultraviolet radiation can cause long-term health issues such as respiratory problems and eye damage.
Moreover, working in confined spaces and at great heights further increased the potential for accidents and injuries.
Furthermore, skilled welders were often in high demand, leading to labor shortages and higher labor costs. This created a bottleneck in industries reliant on welding, as the availability of qualified welders limited their capacity to meet market demands.
To address these challenges, the role of robotics in Australian welding has gained significant importance. Robotic welding systems offer several advantages, including enhanced productivity, improved quality, and increased worker safety.
Robots can perform repetitive welding tasks for extended periods without experiencing fatigue, ensuring consistent and high-quality welds. They can also operate in hazardous environments, reducing the potential for human exposure to dangerous fumes, heat, and radiation.
Additionally, robotic welding systems can work 24/7, eliminating the limitations of human shifts and increasing productivity.
With advanced sensory technologies, robots can detect flaws and adjust welding parameters in real-time, resulting in fewer errors and improved efficiency.
The integration of robotics in Australian welding has also helped alleviate the labor shortage challenges.
Robotic systems can work alongside human welders, complementing their skills and increasing the overall welding capacity of industries.
Therefore, the historical evolution of welding techniques in Australia has seen significant advancements. However, the challenges faced by human welders in terms of productivity and safety have highlighted the need for robotics in the industry.
The adoption of robotic welding systems offers numerous benefits, including increased productivity, improved quality, and enhanced worker safety.
The emergence of robotics in Australian welding
Introduction to Robotic Welding Systems
Robotic welding systems have become increasingly prevalent in the Australian welding industry.
These automated machines, which utilize the latest advancements in robotics technology, have revolutionized the way welding projects are carried out.
With their ability to perform precise and consistent welds, robots have quickly become an essential tool for many Australian welders.
One of the key components of a robotic welding system is the robot arm. These arms are equipped with a welding gun and built-in sensors that allow them to accurately position and manipulate the welding torch.
The robot arm is connected to a computerized control system that directs its movements, ensuring precise and efficient welds.
Robotic welding systems offer numerous advantages over traditional welding methods. Firstly, robots can work at a much faster pace than human welders. They can continuously perform welds without the need for breaks or shift changes, leading to significant time savings.
This increased productivity allows for faster project completion and shorter lead times for customers.
Additionally, robotic welding systems can consistently produce high-quality welds. The precision and accuracy of robot arms ensure that each weld is executed with the same level of proficiency.
This consistency results in stronger and more reliable welds, reducing the risk of defects or failures in the finished product. Furthermore, robotic systems are not prone to fatigue or human error, which can often occur with manual welding, further ensuring weld quality.
Advantages offered by robotic welding compared to traditional methods
Another advantage of robotic welding is improved safety. With robots taking over the welding process, human welders are no longer exposed to the hazards associated with welding, such as fumes, heat, and the risk of injury.
This not only increases the overall safety of the workplace but also improves the health and well-being of the workers.
Stand Out with a Resume That Gets Results
Your career is worth more than a generic template. Let us craft a resume and cover letter that showcase your unique strengths and help you secure that dream job.
Get HiredMoreover, robotic welding systems offer increased flexibility. These machines can be easily programmed to perform various welding tasks, adapting to different project requirements.
Their ability to handle complex welding patterns and execute precise movements allows for greater versatility in welding designs. This flexibility enables welders to take on a wider range of projects and accommodate a diverse clientele.
In addition to these advantages, the implementation of robotic welding systems can also lead to cost savings for welding businesses.
While the initial investment in robotic equipment may be substantial, the long-term benefits outweigh the costs.
The increased productivity, efficiency, and accuracy of robotic welding systems result in reduced labor costs and material wastage. This translates into higher profitability for businesses in the long run.
In general, the emergence of robotics in Australian welding has significantly transformed the industry.
Robotic welding systems offer a multitude of advantages over traditional methods, including increased productivity, consistent weld quality, improved safety, and enhanced flexibility.
With its potential for cost savings and improved profitability, it is no surprise that robotic welding has become an integral part of the Australian welding landscape.
The Impact of Robotics on the Welding Industry in Australia
In recent years, the use of robotics in the welding industry has revolutionized the way welding is performed in Australia. The introduction of robotic systems has had a significant impact on the efficiency, accuracy, and safety of the welding process.
Increased Efficiency and Productivity
One of the primary advantages of integrating robotics in welding is the increased efficiency and productivity it offers.
Robotic systems are capable of working 24/7 without the need for breaks or rest, resulting in constant production and reduced downtime.
Moreover, robots are much faster than human welders. They can perform welds at a consistent speed without compromising on quality.
This increased efficiency allows companies to complete welding projects in shorter timeframes, ultimately boosting overall productivity.
Improved Accuracy and Precision in Welds
Robotic welding systems are equipped with advanced sensors and algorithms that ensure perfect welds every time. These systems can analyze and adjust welding parameters, such as voltage, current, and speed, to achieve precise and accurate welds.
Human welders are prone to inconsistencies and errors due to fatigue, distractions, or varying skill levels. In contrast, robots can consistently repeat welding processes with utmost precision, resulting in high-quality welds that meet stringent industry standards.
Reduced Need for Human Intervention and Associated Safety Risks
One of the most significant advantages of robotics in welding is the reduced need for human intervention. Traditional welding processes often involve human welders working in hazardous environments, exposing them to various safety risks.
By employing robotic systems, companies can improve workplace safety by eliminating or minimizing human presence in dangerous welding areas. Robots can handle the entire welding process autonomously, reducing the likelihood of accidents and injuries.
Additionally, robots can access and operate in confined spaces or extreme temperatures that may pose risks to human welders. This ability expands the possibilities for welding applications and opens up new opportunities for industries such as aerospace and automotive.
In review, the integration of robotics in the welding industry has had a profound impact on Australia’s welding sector. The increased efficiency and productivity, improved accuracy and precision, and reduced safety risks have transformed the way welding operations are conducted.
As robotics technology continues to advance, it is expected that the role of robots in welding will only become more significant.
The welding industry in Australia must embrace and adapt to these advancements to stay competitive and meet the evolving demands of the modern era.
Read: Plumbing 101: A Beginner’s Guide in Australia
Transform Your LinkedIn for Maximum Impact
Elevate your professional brand with a LinkedIn profile that attracts recruiters, showcases your expertise, and maximizes opportunities. Stand out in your industry with a profile built for success.
Boost ProfileCase studies and examples of robotic welding applications in Australia
Automotive industry
In the automotive industry, robotic welding plays a crucial role in various applications.
Robots are used to weld car frames, ensuring precision and consistency in the assembly process.
They are equipped with advanced sensors and programming to perform intricate welds on different materials.
This automation not only enhances productivity but also improves the overall quality of the welding process.
Robotics in the automotive sector have significantly reduced welding defects, resulting in cost savings for manufacturers.
Construction and infrastructure projects
In construction and infrastructure projects, robotic welding has revolutionized the fabrication process.
Robots are utilized for welding large metal structures like bridges and buildings, ensuring strong and reliable connections.
These robots can navigate complex designs and handle heavy workloads, allowing for faster completion of projects.
They offer improved safety by eliminating the need for human welders to work in hazardous environments.
Robotic welding in construction has increased efficiency, reduced errors, and minimized project timelines.
Manufacturing sector
The manufacturing sector extensively relies on robotic welding for a wide range of applications.
Robots are used to weld various components, such as metal sheets, pipes, and structural parts.
They provide exceptional accuracy, repeatability, and consistency, leading to high-quality welds.
These robots can handle repetitive tasks with minimal errors, resulting in increased productivity and reduced labor costs.
Robotic welding has positively influenced the competitiveness and profitability of many manufacturing companies in Australia.
Generally, robotic welding has proven to be invaluable in various sectors in Australia.
The automotive industry benefits from the precision and consistency achieved through robotic welding, reducing defects and improving overall quality.
In construction and infrastructure projects, robotic welding enables faster completion, enhanced safety, and reliable connections.
The manufacturing sector experiences increased productivity and cost savings due to the accuracy and efficiency of robotic welding.
Overall, the role of robotics in Australian welding is essential for technological advancements, improved productivity, and safer working environments.
Read: Top Plumbing Trends in Australian Engineering
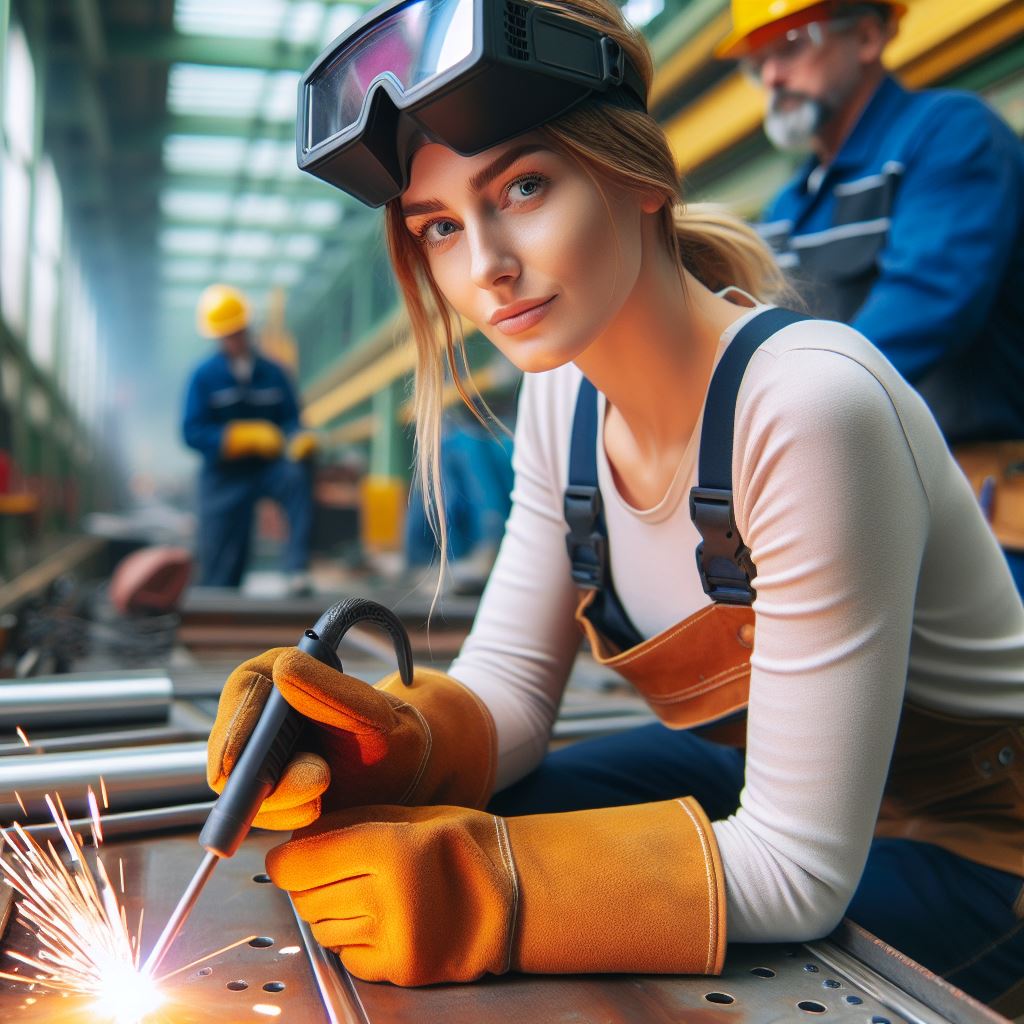
Potential challenges and limitations of robotics in welding
Initial investment costs and implementation challenges
Implementing robotics in welding requires a significant financial investment, which can act as a barrier for some businesses.
Training employees on how to operate and maintain robotic welding systems is essential but can be time-consuming and costly.
There may also be challenges in integrating robots into existing welding processes and ensuring compatibility with other equipment and systems.
Skill requirements for programming and operating robotic welding systems
Programming and operating robotic welding systems require specialized skills that not all welders possess.
Training welders to use these systems effectively and ensuring their proficiency is crucial for successful implementation.
Additionally, the complexity of programming robots for various welding tasks may require expertise from robotic engineers or technicians.
Limitations in adapting to complex welding tasks and materials
While robotics can handle many repetitive welding tasks with precision, they may face limitations in complex welding projects.
Welding processes involving unique materials or non-standard joint configurations can be challenging for robot systems to adapt to.
Human welders may still be needed for specialized welding tasks that require judgment, creativity, or a high level of dexterity.
Potential issues with equipment maintenance and downtime
Robotic welding systems, like any machinery, require regular maintenance to ensure optimal performance.
Ensuring the availability of spare parts and qualified technicians for repairs and maintenance can be a potential challenge.
Equipment breakdowns or malfunctions can lead to significant production downtime, affecting overall productivity and profitability.
Workforce resistance and job displacement concerns
Introducing robotics in welding may face resistance from the existing workforce who fear job displacement.
Addressing these concerns and fostering a positive work environment where humans and robots collaborate is crucial.
Implementing training programs that help current welders transition to operating and maintaining robotic systems can mitigate these concerns.
Safety considerations and regulatory compliance
Ensuring the safety of human workers working alongside robots is a critical challenge in implementing robotic welding systems.
Complying with existing safety regulations and developing new guidelines specific to robotic welding is essential.
The risk of accidents or injuries must be minimized through proper risk assessments, safety protocols, and ongoing monitoring.
Essence, while robotics holds immense potential for improving welding processes in Australia, various challenges and limitations need to be addressed.
From initial investment costs and implementation challenges to skill requirements and limitations in adapting to complex tasks, careful planning and consideration are crucial.
By acknowledging and resolving these challenges, Australian industries can harness the countless benefits that robotics can bring to the welding sector.
Read: The Future of Plumbing Tech in Australia
Opportunities and Future Prospects for Robotics in Australian Welding
Potential for Job Creation in the Robotics Field
- Robotics in welding can create new job opportunities for skilled technicians and engineers.
- The demand for robotic welders is growing, leading to a need for trained professionals.
- Job roles such as robot operators, programmers, and maintenance technicians can emerge.
- The robotics field has the potential to boost employment rates in the welding industry.
Integration with Other Emerging Technologies like Artificial Intelligence
- Robotics and artificial intelligence can work together to enhance welding processes.
- AI algorithms can improve the accuracy and precision of robotic welding systems.
- Integration with AI can enable robots to adapt and learn from welding patterns.
- This collaboration can result in increased efficiency and reduced human intervention.
- Robotics combined with AI can open up new possibilities for automation in welding.
With the rapid advancements in technology, robotics in Australian welding offers numerous opportunities and promising prospects for the future.
The integration of robotics in welding has the potential to create job opportunities in the robotics field.
Skilled technicians and engineers will have the chance to work with cutting-edge robotic welding systems.
As the demand for robotic welders increases, the need for trained professionals will continue to grow.
Job roles such as robot operators, programmers, and maintenance technicians can emerge, providing employment opportunities.
Moreover, the integration of robotics with other emerging technologies like artificial intelligence can revolutionize welding processes.
By combining robotics and AI, welding systems can experience improved accuracy and precision.
AI algorithms can enhance the capabilities of robotic welders, allowing them to adapt and learn from welding patterns.
As a result, the efficiency of welding operations can be significantly increased, reducing the need for human intervention.
Furthermore, the collaboration between robotics and AI opens up new possibilities for automation in welding.
Robots equipped with AI can make real-time adjustments and optimize welding techniques based on various factors.
This integration can lead to higher productivity, cost savings, and improved overall quality in welding processes.
Essentially, the role of robotics in Australian welding presents vast opportunities and future prospects.
The field holds the potential for job creation and can contribute to the growth of the welding industry.
With integration with technologies like artificial intelligence, robotics can transform welding processes, making them more efficient and advanced.
As technology continues to evolve, the use of robotics in welding will undoubtedly play a crucial role in shaping the future of the industry.
Read: How to Become a Plumber in Australia
Explore Further: Renewable Energy and Aussie Mech Eng
Conclusion
In summary, the impact of robotics on Australian welding has been significant.
The use of robots in welding processes has improved efficiency, accuracy, and safety.
It has also allowed for greater productivity and reduced manual labor in the industry.
Furthermore, the implementation of robotics has led to cost savings for Australian welding companies.
The increased use of automation in welding has also created new job opportunities in the field.
However, the anticipation for further advancements and developments in robotics in welding is high.
Australian welders are eager to see how technology will continue to revolutionize their profession.
There is a hope for improved robotic systems that can handle more complex welding tasks.
Additionally, the integration of artificial intelligence in welding robots is another area with great potential.
With continued innovation, Australian welding is poised to become even more efficient and accurate.
K. The future of welding lies in the seamless collaboration between human welders and robotic systems.
L. By harnessing the benefits of automation, Australia can maintain its competitiveness in the global welding market.
M. As technology evolves, the role of robotics in Australian welding will only continue to expand and transform the industry.