Introduction
Welding is an essential task for Australian professionals, but it requires the right equipment to ensure safety and efficiency. In this blog post, we will discuss the key points regarding welding equipment essentials.
These include the importance of proper equipment, safety considerations, and the different types of welding equipment available.
Additionally, we will explore the benefits of using high-quality equipment and how it impacts the overall welding process.
By the end of this post, you will have a better understanding of the equipment needed to excel in your welding profession while maintaining safety and efficacy.
Understanding the Different Types of Welding Equipment
In Australia, various types of welding processes are commonly used, including MIG, TIG, and stick welding.
- MIG Welding: This process involves feeding a wire electrode through a welding gun, which melts and joins the metals together. The equipment required includes MIG welding machines, welding torches, and gas cylinders.
- TIG Welding: Tungsten Inert Gas (TIG) welding utilizes a tungsten electrode to create the weld. It requires a welding machine, TIG torch, shielding gas, and filler rod.
- Stick Welding: Stick welding, also known as Shielded Metal Arc Welding (SMAW), uses consumable electrodes with a flux coating. It requires a welding machine, electrode holder, electrodes, and a power source.
Each type of welding process has specific equipment requirements. Here’s a breakdown:
MIG Welding Equipment
- Welding Machine: A MIG welding machine is essential for controlling the welding current and voltage.
- Welding Torch: The torch feeds the wire electrode and generates the shielding gas to protect the weld pool.
- Electrodes: MIG welding uses consumable wire electrodes made of various materials, such as stainless steel or aluminum.
- Gas Cylinders: MIG welding typically requires gas cylinders filled with a shielding gas like argon or a mixture of argon and carbon dioxide.
TIG Welding Equipment
- Welding Machine: A TIG welding machine controls the welding current and provides options for pulse or continuous current.
- TIG Torch: This torch holds the tungsten electrode and generates the shielding gas to protect the weld zone.
- Shielding Gas: TIG welding commonly utilizes argon or helium as a shielding gas to prevent contamination.
- Filler Rod: In TIG welding, a filler rod made of the same material as the base metal is used to add material if necessary.
Stick Welding Equipment
- Welding Machine: Stick welding machines, also known as arc welders, provide the necessary current and voltage to create the arc.
- Electrode Holder: This tool connects the welding machine to the electrode and allows for easy manipulation of the electrode during welding.
- Electrodes: Stick welding uses consumable electrodes with a flux coating that provides shielding and allows for better arc stability.
- Power Source: Stick welding can be done using different power sources, including direct current (DC) or alternating current (AC).
It is crucial to select the right equipment based on the specific welding process for several reasons
- The type of equipment you use can significantly impact the quality and efficiency of the welding process.
- Different welding processes require different techniques, and the right equipment facilitates proper execution.
- Improper equipment selection can lead to welding defects, weak joints, or other issues.
- Using the correct equipment ensures the safety of the welder and others in the vicinity.
- Choosing suitable equipment enables welders to work within specified parameters and achieve desired results.
To summarize, understanding the different types of welding equipment and their specific requirements is vital for Australian professionals.
Whether it’s MIG, TIG, or stick welding, selecting the right welding machines, torches, electrodes, and gas cylinders is essential for successful welding projects.
Essential Safety Gear for Welding Professionals
Safety gear is absolutely crucial for welding professionals, as it helps protect them from potential hazards and ensures their well-being in the workplace.
It is essential to invest in high-quality safety equipment to minimize the risk of accidents and injuries. Here are some of the most important safety gear items that every welding professional should have:
Welding helmets
A welding helmet is perhaps the most vital piece of safety equipment that a welder needs. It shields the face, eyes, and neck from harmful radiation, sparks, and debris.
Opting for a helmet with an auto-darkening feature is recommended, as it automatically adjusts to different light levels. Trusted brands like Lincoln Electric, 3M Speedglas, and Miller Electric are known for their high-quality welding helmets.
Welding gloves
Welding gloves are designed to protect the hands from heat, sparks, and electric shocks. They should be made from flame-resistant materials such as leather or Kevlar for maximum protection.
Reinforced palms and fingers provide additional durability and grip. Popular options for welding gloves include brands like Tillman, Revco, and Black Stallion.
Safety glasses
Safety glasses with side shields are essential for safeguarding the eyes against sparks, debris, and harmful UV radiation. Look for glasses that are ANSI Z87.1 certified for optimal impact resistance.
Popular brands such as 3M, Uvex, and Jackson Safety offer a range of safety glasses suitable for welding applications.
Fire-resistant clothing
Welding professionals must wear fire-resistant clothing to protect their bodies from burns caused by sparks and molten metal. Materials like treated cotton, leather, or fire-resistant synthetic blends provide the necessary level of protection.
Brands like Carhartt, Bulwark, and Lapco manufacture fire-resistant clothing suitable for welders.
Investing in high-quality safety gear ensures that welding professionals can work with confidence, knowing that they are well-protected.
While these brands are reputable, it is crucial to check for specific product certifications and customer reviews before making a purchase. Remember, saving money on safety gear is not worth compromising safety.
Generally, safety gear is of utmost importance for welding professionals. Welding helmets, gloves, safety glasses, and fire-resistant clothing are all essential to protect welders from potential hazards.
By choosing high-quality brands and ensuring that the safety gear meets necessary certifications, professionals can prioritize their well-being and minimize the risk of accidents and injuries in the welding environment.
So, never underestimate the significance of investing in top-notch safety gear – it’s a decision that can save lives.
Read: Top Plumbing Trends in Australian Engineering
Welding Accessories to Improve Efficiency
In the world of welding, having the right equipment is essential for professionals to work efficiently and effectively.
While the welding machine is undoubtedly the most important tool, there are several additional accessories that can enhance a welder’s efficiency and productivity.
These accessories assist in holding materials in place, removing slag, and ensuring cleaner welds.
Items such as welding clamps, chipping hammers, wire brushes, and welding magnets
One such accessory is the welding clamp. Welding clamps are designed to securely hold the pieces being welded in place, allowing for more accurate and stable welds.
These clamps come in various sizes and styles, such as C-clamps or locking pliers, providing welders with options to suit their specific needs.
Chipping hammers are another valuable accessory for welders. These hammers feature a sharp point on one end and a chisel-like edge on the other.
They are used to remove slag, which is the residue left behind after a weld is completed. By effectively removing slag, chipping hammers ensure a cleaner weld and improve overall weld quality.
Your Personalized Career Strategy
Unlock your potential with tailored career consulting. Get clear, actionable steps designed for your success. Start now!
Get StartedWire brushes are essential accessories for welders as they help in cleaning the workpiece before welding. These brushes remove rust, dirt, and other debris from the metal surface, ensuring a clean and proper weld.
Wire brushes come in various sizes and bristle types, allowing welders to choose the best brush for their specific application.
How these accessories can assist in holding materials in place, removing slag, and ensuring cleaner welds.
Welding magnets are versatile accessories that assist welders in holding multiple pieces together at various angles. These magnets provide strong and reliable clamping force, making it easier to weld intricate shapes or awkward positions.
Welding magnets are especially useful when working with round or curved objects.
Apart from holding materials in place, removing slag, and ensuring cleaner welds, these accessories also improve a welder’s overall efficiency.
By having the right tools readily available, there is no time wasted searching for makeshift solutions or compromising on the quality of work.
Welders can focus on their tasks without interruptions, resulting in improved productivity and timely completion of projects.
Elevating Welding Safety and Efficiency with Essential Accessories
Furthermore, investing in these welding accessories demonstrates a commitment to safety. When materials are securely held in place, there is a reduced risk of accidents or injuries caused by slippage or shifting during the welding process.
Additionally, clean welds ensure structural integrity and longevity, minimizing the likelihood of future repairs or failures.
Essentially, welding accessories play a crucial role in enhancing a welder’s efficiency and productivity.
Welding clamps, chipping hammers, wire brushes, and welding magnets are valuable tools that assist in holding materials in place, removing slag, and ensuring cleaner welds.
By utilizing these accessories, professionals can work more efficiently, produce higher-quality welds, and ultimately achieve better results in their welding projects.
Read: The Future of Plumbing Tech in Australia
Maintaining and Servicing Welding Equipment
Regular maintenance and servicing of welding equipment is crucial for ensuring optimal performance and safety. Neglecting equipment upkeep can lead to costly repairs, increased downtime, and potential hazards.
Here are some tips on how to clean, inspect, and replace components to keep your welding equipment in top shape:
Clean Your Equipment
Regularly clean your welding equipment, including the welding gun, cables, and connectors, to remove dirt, dust, and debris. Use a clean cloth or brush to wipe away any buildup.
Inspect Welding Tips
Check the condition of your welding tips regularly. Look for signs of wear, such as excessive rounding or pitting. Replace worn-out tips promptly to maintain optimal welding performance.
Examine Nozzles
Inspect the welding nozzle for signs of damage or clogging. Clean any debris or spatter build-up using a wire brush or specialized nozzle cleaning tools. Replace worn-out or damaged nozzles to ensure proper shielding gas flow.
Check Filters
If your welding equipment is equipped with filters, inspect them regularly. Clean or replace filters as recommended by the manufacturer to prevent contaminants from entering the system and affecting weld quality.
Inspect Cables and Connectors
Examine the welding cables and connectors for any signs of damage, such as cuts, fraying, or loose connections. Faulty cables and connectors can lead to power interruptions and compromised weld quality. Replace damaged components immediately.
Lubricate Moving Parts
Some welding equipment, such as wire feeders, may have moving parts that require lubrication. Follow the manufacturer’s guidelines to apply the appropriate lubricant to ensure smooth operation and prevent premature wear.
Keep a Maintenance Schedule
Create a regular maintenance schedule for your welding equipment. Note down cleaning, inspection, and replacement tasks and set reminders to ensure they are performed on time.
Stand Out with a Resume That Gets Results
Your career is worth more than a generic template. Let us craft a resume and cover letter that showcase your unique strengths and help you secure that dream job.
Get HiredDocument Maintenance Activities
Keep a record of all maintenance activities, including cleaning, inspections, and component replacements. This documentation can help track the equipment’s history, identify recurring issues, and provide evidence of proper upkeep
Invest in Professional Servicing
While regular maintenance can be done in-house, consider investing in professional servicing periodically. Professionals can conduct comprehensive inspections, identify potential issues, and perform specialized maintenance tasks that may extend the equipment’s lifespan.
Proper maintenance offers several benefits for welding professionals
- Enhanced Performance: Regular cleaning and component replacements ensure consistent, high-quality welds.
- Extended Equipment Lifespan: Proper upkeep reduces wear and tear, prolonging the lifespan of your welding equipment.
- Reduced Downtime: Regular maintenance minimizes the risk of unexpected equipment failures and reduces downtime.
- Improved Safety: Well-maintained equipment reduces the potential risks of accidents, ensuring a safer working environment.
- Cost Savings: By preventing major repairs and early equipment replacements, regular maintenance helps save money in the long run.
On the other hand, neglecting equipment upkeep can result in various risks
- Decreased Performance: Dirty or worn-out components can lead to inconsistent welds and decreased productivity.
- Increased Maintenance Costs: Ignoring regular maintenance may lead to costly repairs or premature equipment replacements.
- Unplanned Downtime: Equipment failures due to neglected maintenance can result in unexpected production delays.
- Compromised Safety: Faulty equipment poses a safety risk to operators and others in the vicinity.
- Inconsistent Weld Quality: Neglected equipment may produce inconsistent welds, affecting the overall quality of the work.
Overall, prioritizing regular maintenance and servicing is essential for Australian welding professionals.
By following these tips and ensuring proper upkeep, professionals can achieve optimal performance, reduce risks, and extend the lifespan of their welding equipment.
Read: A Day in the Life of an Aussie Plumber
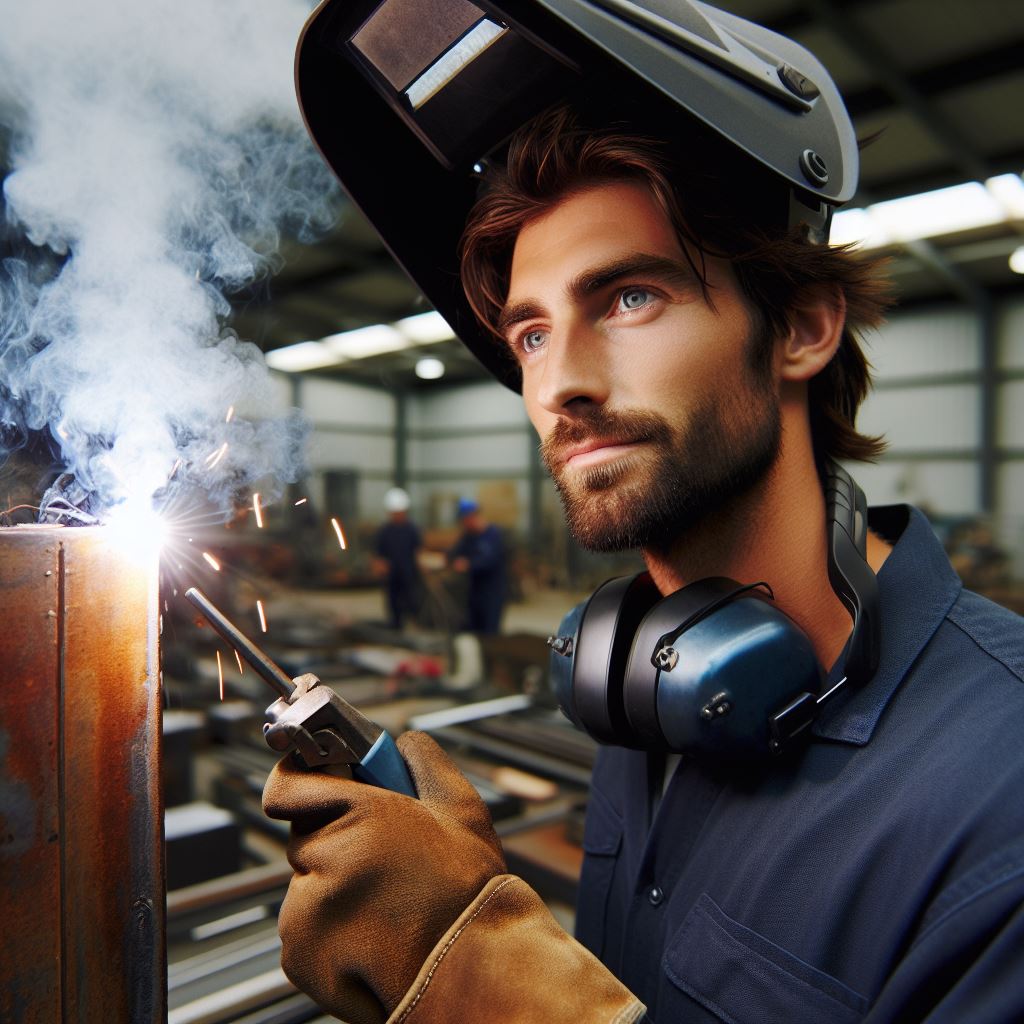
Learn More: Landscaping Laws in Australia Explained
Choosing Quality Australian Welding Equipment Suppliers
When it comes to purchasing welding equipment, choosing reputable Australian suppliers is crucial. Not only does it ensure the quality of the products, but it also provides peace of mind and after-sales support.
Here are some factors to consider when selecting the right supplier for your welding needs:
Product Quality
The first and most important factor to consider is the quality of the welding equipment.
Look for suppliers who offer high-quality products that are durable, reliable, and safe to use. Check if they comply with Australian safety standards and have the necessary certifications.
Customer Reviews
Reading customer reviews and testimonials can give you insight into the reputation of the supplier. Look for feedback from other professionals in the welding industry to get an idea of their experiences with the supplier and the equipment they offer.
Positive reviews indicate a trustworthy supplier.
Warranties
Reputable Australian suppliers of welding equipment often provide warranties for their products. A warranty ensures that you are protected against any manufacturing defects or faults in the equipment.
It is essential to inquire about the length and coverage of the warranty before making a purchase.
After-Sales Support
Good after-sales support is vital when purchasing welding equipment.
Choose a supplier that offers excellent customer service, technical assistance, and spare parts availability. Having access to support after your purchase can save you time and money in the long run.
Trusted Suppliers and Brands
Here is a list of trusted Australian welding equipment suppliers or specific brands that cater to the needs of professionals in the industry:
- Advanced Welding Supplies
- WESCO
- Kemppi
- Lincoln Electric
- ESAB
These suppliers have a proven track record and offer a wide range of welding equipment suitable for various applications. It is recommended to explore their products and services further to find the right fit for your welding needs.
Choosing quality Australian welding equipment suppliers is essential for professionals who rely on their tools to deliver top-notch results.
By considering factors such as product quality, customer reviews, warranties, and after-sales support, you can make an informed decision and invest in reliable equipment that will enhance your welding capabilities.
Read: How to Become a Plumber in Australia
Transform Your LinkedIn for Maximum Impact
Elevate your professional brand with a LinkedIn profile that attracts recruiters, showcases your expertise, and maximizes opportunities. Stand out in your industry with a profile built for success.
Boost ProfileUncover the Details: Welding Art: A Creative Path in Australia
Discover More: Essential Skills for Aussie Mech Engineers
Conclusion
In closing, this blog section highlighted the essential factors to consider when selecting welding equipment for Australian professionals.
We discussed the importance of investing in the right equipment that prioritizes safety, efficiency, and quality.
By choosing high-quality welding equipment, professionals can ensure better work outcomes and a safer work environment.
It is crucial to prioritize safety and efficiency to meet industry standards and achieve optimal results.
Whether it is choosing the right welding machine, protective gear, or accessories, professionals should carefully evaluate their needs and invest wisely.
By doing so, they can enhance productivity, reduce downtime, and improve the overall welding experience.
Therefore, Australian professionals must make informed decisions while selecting welding equipment that best meets their requirements.