Introduction
Risk management in supply chains refers to the process of identifying, assessing, and mitigating risks.
Effective risk management is crucial for ensuring the smooth operation of supply chains and avoiding disruptions.
This blog post provides a comprehensive overview of risk management in supply chains, including its definition, importance, and an outline of the upcoming content.
Definition of risk management in supply chains
Risk management in supply chains involves identifying potential risks, evaluating their impact and likelihood, and implementing strategies to minimize or eliminate them.
Importance of effective risk management
Effective risk management helps businesses maintain a competitive edge by minimizing disruptions, reducing costs, and ensuring the reliability of their supply chains.
Overview of the blog post
This blog post will cover various aspects of risk management in supply chains, including risk assessment techniques, strategies for mitigating risks, and case studies showcasing successful risk management practices.
Some of the specific topics that will be discussed include supply chain vulnerabilities, impact of globalization, the role of technology in risk management, and the importance of collaboration among supply chain partners.
Basically, risk management in supply chains is crucial for businesses to ensure operational efficiency and minimize potential disruptions.
The following sections will delve deeper into different aspects of risk management, providing valuable insights and practical guidance for businesses looking to enhance their supply chain resilience. Stay tuned for the upcoming content!
Common Risks in Supply Chains
Supply chain disruptions
- Natural disasters
- Political instability
- Supplier bankruptcy
Demand fluctuations
- Seasonal demand variations
- Unexpected changes in consumer behavior
Quality and safety issues
- Product recalls
- Safety violations
Supply chains are not immune to risks and disruptions. In fact, they are constantly exposed to various challenges that can negatively impact their efficiency and effectiveness. This section will discuss some of the common risks faced by supply chains.
Supply chain disruptions
- Natural disasters can have a significant impact on a supply chain’s operations. Events like earthquakes, hurricanes, or floods can damage infrastructure, disrupt transportation networks, and hamper production and distribution processes.
- Political instability in certain regions can also disrupt supply chains. Conflicts, wars, or political unrest can lead to the closure of borders, restrictions on transportation, and uncertainty in trade agreements, making it difficult for goods to be transported or delivered on time.
- Supplier bankruptcy is another risk that can disrupt the smooth functioning of a supply chain. If a key supplier goes bankrupt, it can lead to delays in the delivery of essential raw materials or components, affecting production schedules and causing financial losses for the company.
Demand fluctuations
- Seasonal demand variations can create challenges for supply chains. Products that are heavily dependent on specific seasons, such as winter apparel or holiday decorations, may experience significant spikes in demand during certain periods, requiring careful planning and coordination to meet customer needs.
- Unexpected changes in consumer behavior can also disrupt supply chains. Shifts in trends, preferences, or buying habits can result in sudden increases or decreases in demand for certain products, catching supply chains off guard and leading to overstocking or stockouts.
Quality and safety issues
- Product recalls can have severe implications for supply chains. If a product is found to be defective or unsafe, it may need to be recalled from the market, leading to disruptions in production, distribution, and customer trust. This can damage a company’s reputation and result in financial losses.
- Safety violations, such as failure to meet regulatory standards or non-compliance with health and safety protocols, can also pose risks to supply chains. Violations can result in fines, legal liabilities, damaged relationships with stakeholders, and even closure of the entire supply chain.
Therefore, supply chains face a wide range of risks that can impact their efficiency and profitability. By identifying and understanding these risks, supply chain managers can implement appropriate risk management strategies to mitigate their impact and ensure smooth operations.
Read: Day in the Life of an Aussie Train Driver
Key Steps in Supply Chain Risk Management
Risk identification
- Mapping the supply chain
- Identifying potential risks and vulnerabilities
Risk assessment
- Quantifying the impact and likelihood of risks
- Prioritizing risks based on their significance
Mitigation
- Developing strategies to reduce or eliminate risks
- Implementing preventive measures
Monitoring and control
- Continuous monitoring of the supply chain for potential risks
- Taking corrective actions when necessary
Response and recovery
- Developing contingency plans
- Establishing communication channels with suppliers and stakeholders
Effective risk management in supply chains is crucial for organizations to ensure smooth operations and minimize potential disruptions.
By following key steps in supply chain risk management, businesses can identify, assess, mitigate, and respond to risks in an efficient and proactive manner. This section will discuss the key steps involved in supply chain risk management
Risk identification
The first step in supply chain risk management is to identify the potential risks and vulnerabilities in the supply chain.
This can be done by mapping the entire supply chain, including all the components and entities involved.
Once the supply chain is mapped, organizations can identify potential risks such as supplier failures, natural disasters, transportation delays, and geopolitical instability. It is important to consider both internal and external factors that may impact the supply chain.
Risk assessment
After identifying potential risks, organizations need to assess the impact and likelihood of each risk. This involves quantifying the potential consequences and probability of occurrence.
By assessing risks, organizations can prioritize them based on their significance. Risks with higher potential impact and likelihood should be given more attention and resources for mitigation.
Risk mitigation
Once risks are identified and assessed, organizations need to develop strategies to reduce or eliminate these risks. This may involve selecting alternate suppliers, improving transportation networks, or diversifying sourcing locations.
Implementing preventive measures is essential to minimize the likelihood of risks occurring. This can include establishing quality control processes, conducting regular audits, and implementing supply chain visibility systems.
Your Personalized Career Strategy
Unlock your potential with tailored career consulting. Get clear, actionable steps designed for your success. Start now!
Get StartedMonitoring and control
Supply chain risks are dynamic and can change over time. Continuous monitoring of the supply chain is necessary to identify new risks and assess the effectiveness of existing risk mitigation strategies.
If a potential risk is identified or an existing risk escalates, organizations must take corrective actions promptly. This may involve adjusting inventory levels, revising production schedules, or finding alternative suppliers.
Response and recovery
Despite thorough risk management efforts, disruptions may still occur. Organizations need to develop contingency plans to respond to unexpected events and expedite recovery.
Establishing communication channels with suppliers and stakeholders is essential during a risk event. Clear and timely communication can help coordinate response efforts, minimize further damage, and facilitate recovery.
In review, effective supply chain risk management involves identifying, assessing, mitigating, monitoring, and responding to risks in a proactive manner.
By following key steps, organizations can ensure the resilience and continuity of their supply chains, improving overall business performance.
Read: Trucker Tales: Stories from the Road
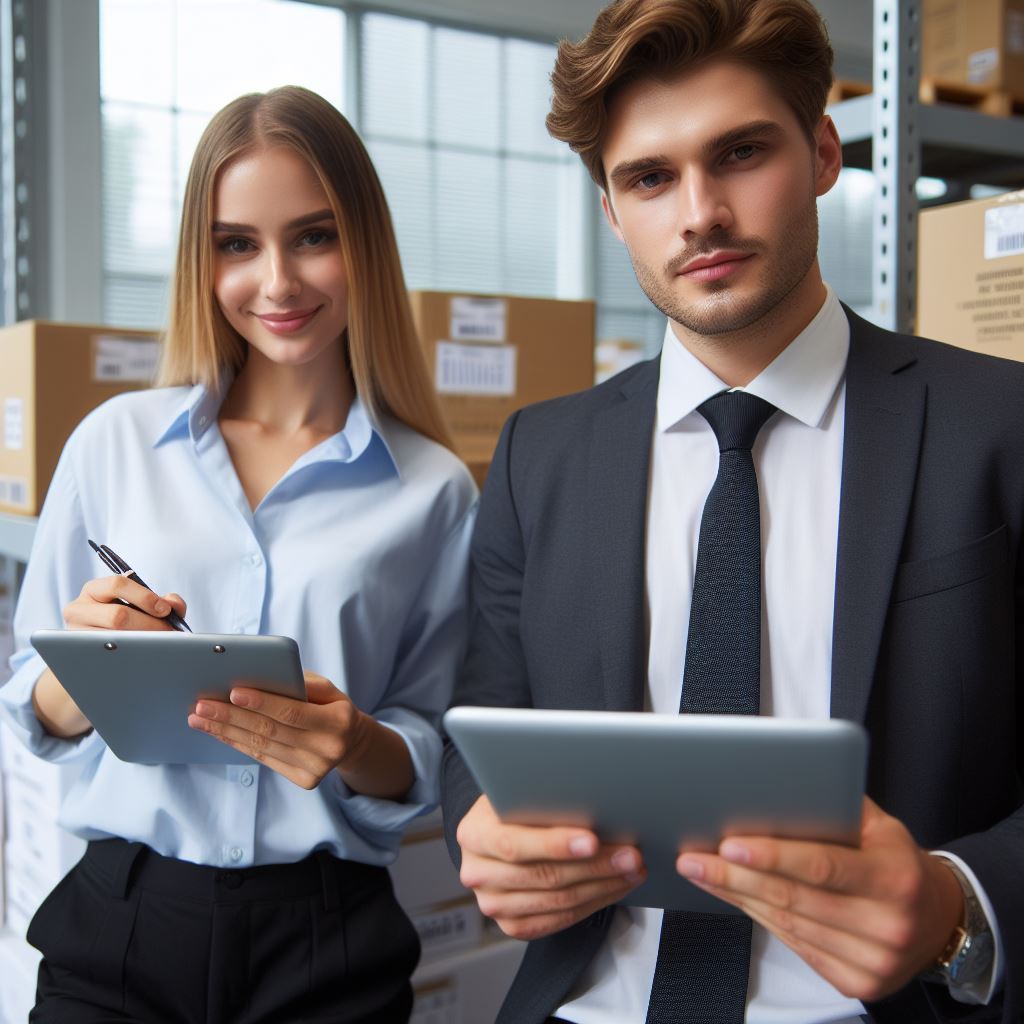
See Related Content: Flight Attendant Training: What to Expect in Aus
Best Practices for Supply Chain Risk Management
Collaborative relationships with suppliers
- Building strong supplier relationships
- Promoting transparency and open communication
Diversification of suppliers
- Reducing dependence on a single supplier
- Ensuring alternative supplier options
Inventory management
- Maintaining adequate safety stock
- Considering lean inventory practices
Technology and data analytics
- Utilizing advanced supply chain management systems
- Analyzing real-time data for risk assessment and decision-making
Supply chain risk management is a critical aspect of ensuring the smooth operation and resilience of a company’s supply chain.
In today’s interconnected global economy, supply chains are vulnerable to various risks, including natural disasters, political instability, and disruptions in transportation and logistics.
It is essential for organizations to adopt best practices to proactively manage these risks and minimize their impact on business operations. This section explores some of the best practices for effective supply chain risk management.
Collaborative relationships with suppliers
Building strong relationships with suppliers is crucial for effective supply chain risk management. Organizations should establish trust and mutual understanding with their suppliers to foster collaboration and facilitate timely risk identification and mitigation.
Regular communication and sharing of information can help identify potential risks and develop strategies to address them before they escalate into significant disruptions. Promoting transparency in the supply chain can also improve visibility and enable proactive risk management.
Diversification of suppliers
Reducing dependence on a single supplier is a vital risk mitigation strategy. By diversifying their supplier base, organizations can minimize the impact of disruptions caused by a supplier’s inability to deliver goods or services.
This can involve identifying and engaging with multiple suppliers who can provide similar products or services. Having alternative supplier options ensures continuity of supply and reduces the risk of production delays or customer dissatisfaction.
Inventory management
Effective inventory management is essential for mitigating the impact of supply chain disruptions. Maintaining adequate safety stock can help buffer against unexpected demand fluctuations or disruptions in the supply chain.
Organizations should regularly analyze demand patterns and lead times to determine optimal stock levels. Additionally, implementing lean inventory practices can minimize the carrying cost of inventory while ensuring timely fulfillment of customer orders.
Technology and data analytics
The use of technology and data analytics can significantly enhance supply chain risk management. Advanced supply chain management systems can provide real-time visibility into inventory, demand, and supplier performance.
By leveraging real-time data, organizations can assess risks, identify potential disruptions, and make informed decisions to mitigate them. Predictive analytics can also help identify early warning signs of potential risks, allowing for proactive risk mitigation measures.
In fact, implementing best practices for supply chain risk management is crucial for organizations to minimize the impact of disruptions and ensure the resilience of their supply chains.
Collaborative relationships with suppliers, diversification of suppliers, effective inventory management, and the use of technology and data analytics are key strategies that organizations should adopt to proactively manage risks.
By proactively identifying and addressing potential risks, organizations can protect their supply chains and maintain operational efficiency even in the face of uncertainties and disruptions.
Read: Salary Insights for Train Drivers in Oz
Case Studies: Successful Supply Chain Risk Management Examples
Example 1: Aussie Logistics’ response to a major supplier bankruptcy
- Aussie Logistics implemented strategies to minimize disruption caused by the supplier bankruptcy.
- Lessons were learned from the experience to enhance future risk management practices.
Down Under Manufacturing’s proactive approach to supply chain disruptions
- Down Under Manufacturing made investments in risk assessment and mitigation measures to prevent disruptions.
- Effective risk management by Down Under Manufacturing resulted in positive outcomes.
Supply chains are vulnerable to various risks, including supplier bankruptcy, natural disasters, and geopolitical uncertainties. In this section, we will examine two real-life case studies that demonstrate successful supply chain risk management strategies.
Aussie Logistics’ response to a major supplier bankruptcy
When one of Aussie Logistics’ major suppliers declared bankruptcy, it posed a significant threat to their supply chain. However, the company proactively implemented several key strategies to minimize disruption:
Stand Out with a Resume That Gets Results
Your career is worth more than a generic template. Let us craft a resume and cover letter that showcase your unique strengths and help you secure that dream job.
Get Hired- Aussie Logistics diversified its supplier base to reduce reliance on a single source.
- They established long-term contracts with multiple suppliers to ensure continuity.
- Regular communication and close collaboration with suppliers helped identify warning signs.
- A contingency plan was in place, allowing for quick sourcing alternatives when needed.
These strategies enabled Aussie Logistics to mitigate the impacts of the supplier bankruptcy, minimizing disruption and ensuring business continuity. However, they also learned valuable lessons from the experience:
- Periodic assessments of supplier financial health are crucial to early identification of risks.
- Building strong relationships and open communication channels with suppliers enhances risk management.
- Continuous evaluation and improvement of contingency plans are necessary for adapting to changing circumstances.
Example 2: Down Under Manufacturing’s proactive approach to supply chain disruptions
Down Under Manufacturing, anticipating potential supply chain disruptions, took a proactive approach to risk management
- They invested in advanced risk assessment technology to identify vulnerabilities throughout the supply chain.
- Regular audits and assessments of suppliers’ risk management practices were conducted.
- Down Under Manufacturing implemented mitigation measures, such as redundancies in the supply network and safety stock.
- They collaborated closely with suppliers to enhance communication and align risk management strategies.
These efforts paid off, resulting in positive outcomes for Down Under Manufacturing:
- Minimized disruptions and improved overall supply chain resilience.
- Enhanced ability to predict and respond to potential risks, thereby reducing financial losses.
- Increased customer satisfaction through reliable and uninterrupted product delivery.
These case studies demonstrate the significance of proactive risk management in supply chains. By implementing strategic measures and learning from past experiences, companies can effectively mitigate disruptions and build resilient supply chains.
Read: Train Driving: Skills You Need in Australia
Gain More Insights: Networking Tips for Logistics Professionals
Gain More Insights: Train Driver Licenses in Australia Explained
Conclusion
Effective risk management is indispensable for safeguarding supply chains against potential disruptions.
By proactively identifying and addressing vulnerabilities, companies can enhance resilience and maintain operational continuity.
Supply chains are susceptible to various threats, including natural disasters, geopolitical instability, and economic downturns.
However, with robust risk management strategies in place, organizations can mitigate the impact of these risks and ensure smooth operations.
The COVID-19 pandemic underscored the importance of agility and adaptability in supply chain risk management.
Companies that prioritize risk management practices gain a competitive edge in volatile markets by effectively responding to unforeseen events.
From supply chain mapping to scenario planning, risk management requires a comprehensive and proactive approach.
Technology plays a pivotal role in enabling real-time visibility and data-driven decision-making to mitigate risks effectively.
By embracing innovative solutions and best practices, companies can enhance their supply chain resilience and responsiveness.
Continuous monitoring and evaluation are essential to identify emerging risks and adjust risk management strategies accordingly.
Collaboration across stakeholders and supply chain partners is critical for enhancing risk management effectiveness.
By fostering open communication and sharing insights, organizations can collectively strengthen their risk mitigation efforts.
As supply chains become increasingly interconnected and complex, the importance of robust risk management practices cannot be overstated.
Successful risk management requires a proactive mindset and a commitment to continuous improvement.
By investing in risk management capabilities and fostering a culture of resilience, organizations can navigate uncertainty and thrive in dynamic environments.
In today’s rapidly evolving business landscape, risk management is not just a necessity—it’s a strategic imperative for sustainable success.
As we move forward, let us remain vigilant and proactive in managing risks to ensure the resilience and longevity of our supply chains.