Introduction
Embarking on the journey of MIG vs TIG welding, we explore their unique attributes. In Australia’s dynamic industry, choosing the right welding technique is pivotal.
MIG, with its speed and efficiency, suits large-scale projects. Meanwhile, TIG’s precision and versatility make it ideal for intricate work.
As we delve into the nuances of these methods, consider their environmental impact and cost-effectiveness.
Australia’s welding landscape demands a thoughtful approach, taking into account factors like metal thickness, project size, and welding conditions.
Join us in this exploration to make an informed decision, ensuring your welding practices align with Australia’s industrial demands.
Definition and Explanation of MIG Welding
What is MIG welding? MIG welding, also known as Metal Inert Gas welding, is a welding process where an electric arc forms between a consumable electrode wire and the workpiece.
The electrode wire melts and joins the metals together, creating a strong bond.
Advantages of MIG Welding
- MIG welding allows for faster welding and higher productivity due to its continuous wire feed.
- It provides a cleaner weld as the shielding gas protects the weld pool from atmospheric contaminants.
- MIG welding is versatile as it can be used on a wide range of metals, including stainless steel, aluminum, and mild steel.
- It is relatively easier to learn and operate, making it suitable for both beginners and experienced welders.
Disadvantages of MIG Welding
- MIG welding equipment can be more expensive compared to other welding processes.
- It requires a constant supply of shielding gas, which can add to the overall cost of the welding operation.
- MIG welding may not be suitable for thick materials as it may result in incomplete or shallow penetration.
- It produces more spatter compared to other welding processes, requiring additional post-weld cleaning.
Applications and Industries where MIG Welding is Commonly Used in Australia
MIG welding is widely used across various industries in Australia due to its versatility and efficiency. Some common applications include:
- Automotive industry: MIG welding is commonly used in the production and repair of car bodies, exhaust systems, and engine components.
- Construction industry: It is used for welding structural components, such as beams, columns, and joints.
- Manufacturing industry: MIG welding is utilized in the fabrication of metal furniture, appliances, and machinery.
- Shipbuilding industry: MIG welding is crucial in constructing ships and offshore structures, ensuring strong and durable welds.
- Maintenance and repair: MIG welding is valuable for repairing metal structures, equipment, and machinery.
MIG welding is a widely used welding process in Australia due to its versatility, efficiency, and ability to provide clean welds.
While it has its disadvantages, the advantages outweigh them for many applications and industries.
Its usage in the automotive, construction, manufacturing, shipbuilding, and maintenance sectors further highlight its significance in the Australian welding industry.
TIG (Tungsten Inert Gas) welding, also known as GTAW (Gas Tungsten Arc Welding), is a welding process that uses a non-consumable tungsten electrode to create the weld.
It is commonly used in various industries in Australia due to its versatility and precision. TIG welding offers several advantages and disadvantages, making it important to consider its suitability for different applications.
Read: Top Plumbing Trends in Australian Engineering
Definition of TIG Welding
TIG welding is a fusion welding process that involves creating a high-temperature arc between the tungsten electrode and the workpiece.
The weld pool is formed by the melting of the workpiece and the addition of filler material, if necessary. Unlike other welding methods, TIG welding does not require a flux or filler wire that burns during the process.
The Process of TIG Welding
TIG welding begins with the preparation of the workpiece and the electrode. The electrode, made of tungsten, is sharpened to a fine point to control the heat concentration.
The arc is ignited by striking it against the workpiece, and an inert gas, such as argon, is used to shield the weld zone from atmospheric contamination.
The welder holds the electrode with one hand and uses the other hand to feed the filler wire into the weld pool, if needed. The heat from the arc melts the workpiece and the filler material, creating a weld bead.
TIG welding allows for precise control over the welding process, resulting in high-quality welds with minimal spatter.
Advantages of TIG Welding
- TIG welding produces clean and aesthetically appealing welds with a low level of spatter.
- It allows for precise control over the welding process, making it suitable for thin materials and intricate welds.
- Due to the absence of flux and the use of inert gas, TIG welding produces welds with minimal porosity.
- TIG welding can be used to weld a wide range of materials, including stainless steel, aluminum, and copper alloys.
- It provides better heat control compared to other welding methods, reducing the risk of distortion or warping.
Disadvantages of TIG Welding
- TIG welding requires a high level of skill and expertise, making it more time-consuming and costly.
- It has a slower welding speed compared to other methods, making it unsuitable for large-scale production.
- The process is sensitive to wind or drafts, which can disrupt the shielding gas, affecting the quality of the weld.
- TIG welding may require the use of specialized equipment, such as a foot pedal control for precise current adjustment
- Due to the need for manual feeding of filler material, TIG welding can be challenging for beginners or inexperienced welders.
Applications of TIG Welding in Australia
TIG welding is commonly used in various industries in Australia, including:
- Aerospace: TIG welding is preferred for its ability to create high-quality welds on thin materials used in aircraft components.
- Automotive: TIG welding is used for precision welding of exhaust systems, engine components, and aluminum body panels.
- Oil and Gas: TIG welding is suitable for welding pipelines, pressure vessels, and other critical components in the industry.
- Food and Beverage: TIG welding is used for sanitary welding of stainless steel tanks and equipment in the food processing industry.
- Artistic Fabrication: TIG welding allows artists and fabricators to create intricate and visually appealing metal sculptures and designs.
Essentially, TIG welding is a versatile welding process commonly used in various industries in Australia. It offers precise control, clean welds, and the ability to weld a wide range of materials.
However, it requires a high level of skill and may not be suitable for large-scale production. Understanding the advantages, disadvantages, and applications of TIG welding is crucial in determining its suitability for specific projects in Australia.
Read: The Future of Plumbing Tech in Australia
See Related Content: Underwater Welding in Australia: Opportunities
Delve into the Subject: Green Energy: Mech Engineers’ New Frontier
Comparison of MIG and TIG Welding
Key Differences between MIG and TIG Welding Techniques
- MIG welding uses a consumable wire electrode, while TIG welding uses a non-consumable tungsten electrode.
- MIG welding is a semi-automatic process, while TIG welding is a manual process.
- MIG welding allows for high deposition rates, whereas TIG welding produces precision welds.
- MIG welding is suitable for thicker metals, while TIG welding is better for thin materials.
Differences in terms of Equipment, Skill Requirements, and Cost
- MIG welding requires a MIG welder, shielding gas, and a wire feeder, which are relatively affordable.
- TIG welding requires a TIG welder, a high-frequency unit, and a foot pedal, making it a more expensive setup.
- Mastering MIG welding technique is relatively easier compared to TIG welding.
- TIG welding demands higher skill levels, precision, and experience in order to produce quality welds.
Analyze the Quality and Strength of Welds Produced by Each Method
- MIG welding produces strong and durable welds with good structural integrity.
- TIG welding creates the highest quality welds that are free from defects and impurities.
- Welds created by TIG welding have excellent appearance, suitable for visible applications.
- MIG welding may result in spatter and distortions, affecting the overall aesthetics of the weld.
Evaluate Efficiency and Productivity in Different Welding Scenarios
- MIG welding is quicker and more efficient for large-scale production and heavy-duty applications.
- TIG welding is slower but offers superior control and precision, making it ideal for intricate work.
- MIG welding is generally faster, completing welds in less time compared to TIG welding.
- TIG welding’s slower pace allows for better heat control, minimizing the risk of distortion.
Basically, choosing between MIG and TIG welding depends on various factors such as the type of materials, project requirements, and skill level.
MIG welding is more suitable for thicker metals, large-scale production, and applications where speed is important. On the other hand, TIG welding excels in creating high-quality, visually appealing welds, especially on thin materials and intricate designs.
While MIG welding may be more cost-effective and easier to learn, TIG welding demands higher skill levels and a larger investment in equipment.
Ultimately, the decision on which welding method is best for Australia relies on considering the specific needs of each welding scenario.
Your Personalized Career Strategy
Unlock your potential with tailored career consulting. Get clear, actionable steps designed for your success. Start now!
Get StartedRead: A Day in the Life of an Aussie Plumber
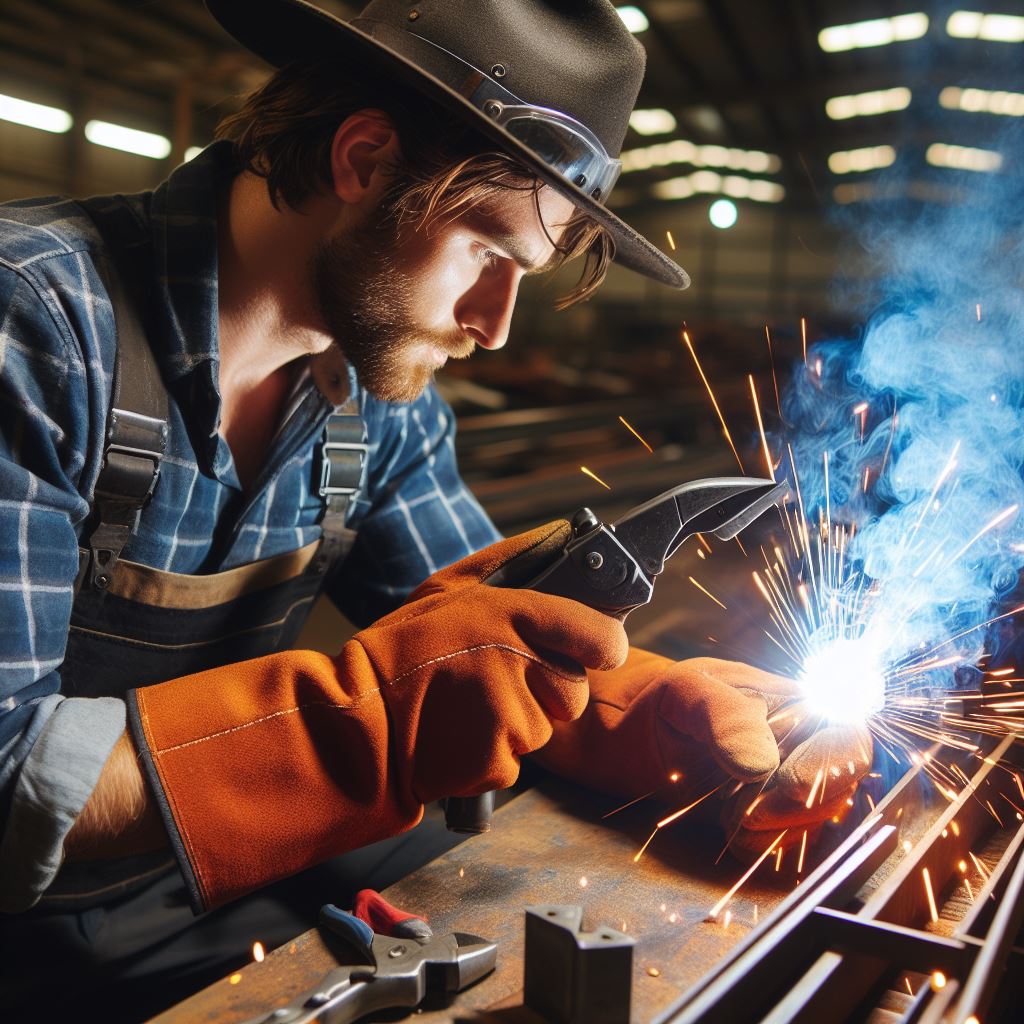
Choosing the Best Option for Australia
Australia’s welding industry has a diverse range of needs and requirements, making it crucial to carefully consider the best welding option.
Both MIG (Metal Inert Gas) and TIG (Tungsten Inert Gas) welding methods have their advantages and disadvantages. In this blog section, we will evaluate various factors to determine their suitability for Australia’s welding industry.
Consider the Specific Welding Needs and Requirements of Australia’s Industry
One of the key factors to consider when choosing a welding method for Australia is the specific needs and requirements of the industry.
Different industries may prioritize different aspects such as cost-effectiveness, speed, precision, and strength. Understanding these priorities is crucial in selecting the most suitable method.
Factors Such as Cost-Effectiveness, Speed, Precision, and Strength
In terms of cost-effectiveness, MIG welding stands out as it is a faster process that requires less skill, making it more affordable in terms of labor costs.
TIG welding, on the other hand, typically requires skilled welders, which can drive up the cost. However, TIG welding offers higher precision and is suitable for intricate projects.
Speed is another important factor. MIG welding is generally faster due to its continuous wire feed, making it ideal for large-scale projects.
TIG welding is slower due to the need for manual filler material. For time-sensitive projects, MIG welding may be the preferred option.
When it comes to strength, both MIG and TIG welding can produce strong welds. However, TIG welding offers superior control over heat input, resulting in stronger joints.
For industries that require exceptionally strong welds, such as aerospace or automotive, TIG welding may be the optimal choice.
Evaluating the Compatibility of MIG and TIG Welding with Materials Used in Australia
Considering the types of materials commonly used in Australia’s industries is essential in selecting the appropriate welding method.
MIG welding is well-suited for welding thick materials like steel and aluminum, which are commonly used in various industries. TIG welding is more versatile and can weld a broader range of materials, including stainless steel, copper, and titanium.
Recommendations for Specific Applications and Industries in Australia
Based on the evaluation of various factors, it is clear that both MIG and TIG welding methods have their advantages and are suitable for different applications and industries in Australia. Here are some recommendations:
- For industries focused on cost-effectiveness and faster production, MIG welding is recommended.
- Industries requiring intricate and precise welds should consider TIG welding.
- For projects that demand exceptionally strong welds, particularly in the aerospace or automotive sectors, TIG welding is the preferred choice.
- Industries working with a variety of materials may benefit from the versatility of TIG welding.
In review, selecting the best welding option for Australia requires careful consideration of specific needs, cost-effectiveness, speed, precision, strength, and material compatibility.
By understanding these factors, industries can make informed decisions for successful welding operations.
Read: How to Become a Plumber in Australia
You Might Also Like: Rural vs Urban Carpentry in Australia
Uncover the Details: Plumbing Codes & Standards in Australia
Conclusion
In closing, we have explored the key differences between MIG and TIG welding methods. We have seen that MIG welding is faster and more suitable for heavy-duty applications, while TIG welding offers superior precision and quality.
It is crucial to choose the right welding method for Australia’s industry, as it can significantly impact the durability and safety of the welded structures.
Considering factors such as the type of material, thickness, and desired outcome is essential in making an informed decision.
Stand Out with a Resume That Gets Results
Your career is worth more than a generic template. Let us craft a resume and cover letter that showcase your unique strengths and help you secure that dream job.
Get HiredWe encourage readers to further explore and research the topic of welding practices in Australia.
By understanding the specific requirements of their industry, they can make informed decisions that will yield the best results and contribute to the overall growth and success of the Australian welding industry.
By choosing the right welding method, Australian businesses can enhance productivity, ensure the longevity of their welded structures, and maintain the highest quality standards.
It is an investment that will pay off in the long run, benefiting both the industry and its customers.
So, take the time to delve deeper into the world of MIG and TIG welding, educate yourself, and make the right choice that suits your specific needs.
The right welding method can be a game-changer for Australia’s industry, offering a competitive edge and setting new benchmarks for excellence.